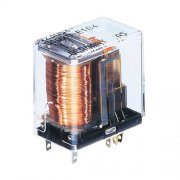
HUIMU Industrial (HUIMULTD) is a global manufacturer and supplier of Solid State Relays, Solid State Moudles, Rectifiers, Automotive Relays, Electronic power relays, and Electrical Signal Relays, with over 20 years experience on industrial control field. More details please visit www.huimultd.com
Electromagnetic Relay - Short essay
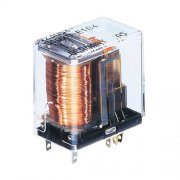
SPDT Solid State Relay - 3.MGR (HUIMULTD) SPDT SOLID STATE RELAY
§3. MGR (HUIMULTD) SPDT Solid State Relay
3.1 How to select MGR (HUIMULTD) SPDT Solid State Relay
1) MGR-1KB series Single Phase AC Solid State Relay
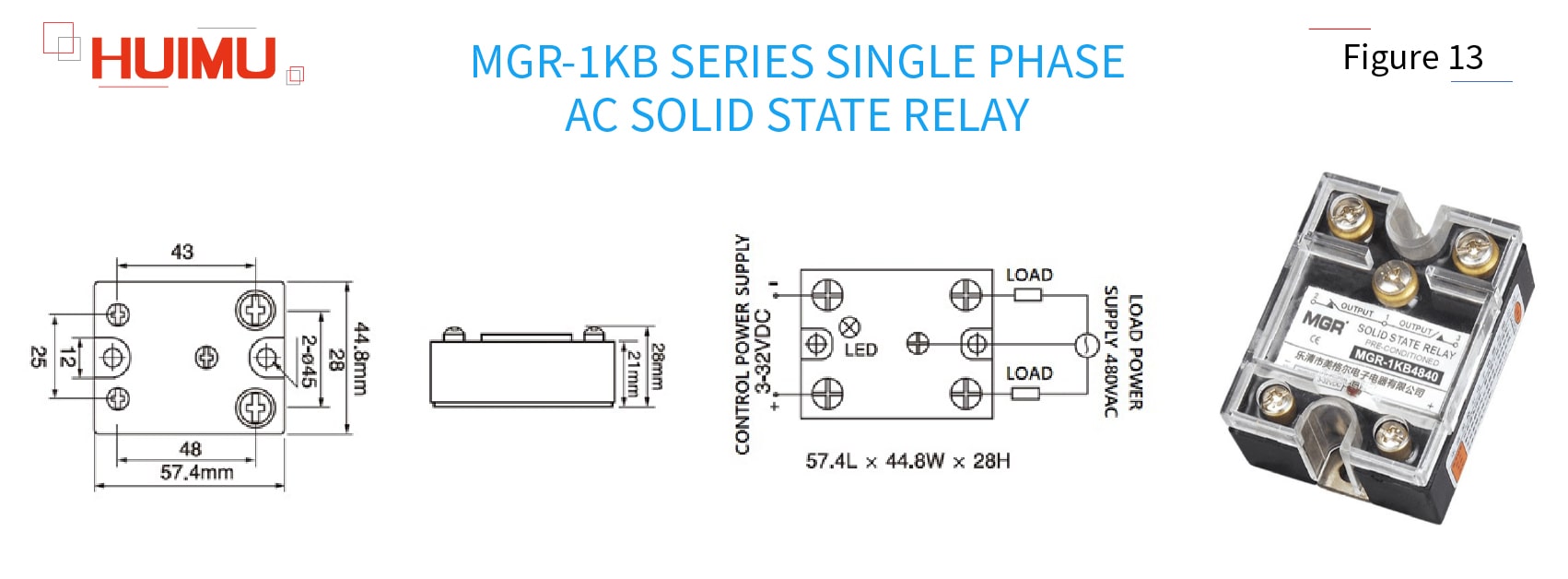
Type meaning:
MGR - 1:[Single phase] - KB:[SPDT (Single Pole, Double Throw)] - 48:[Load voltage 480VAC] - 40:[40A]
Control Voltage:
3~32VDC (such as 3VDC, 5VDC, 9VDC, 12VDC, 18VDC, 24VDC, 32VDC or customized control voltage)
Control Current:
Ultra low input current, ≤20mA
Load Voltage:
Single phase 24~480VAC (such as 24VAC, 48VAC, 110VAC, 230VAC, 380VAC, 480VAC or customized load voltage)
Load Current:
10A, 15A, 20A, 25A, 30A, 40A
Dimensions & Mounting:
57.4mm*44.8mm*28mm; Panel mount solid state relay with transport cover,metal base and screw terminals
2) MGR-1AKB series Single Phase AC Solid State Relay
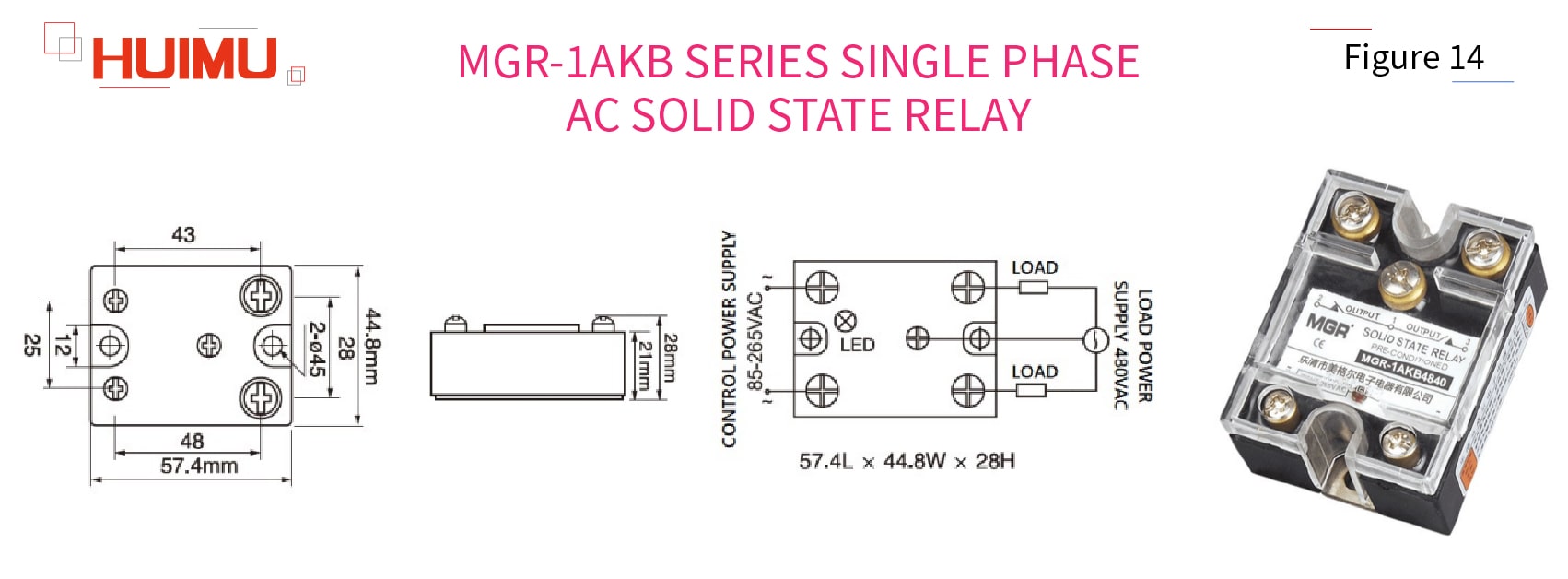
Type meaning:
MGR - 1:[Single phase] - A:[Control voltage 85-265VAC] - KB:[SPDT (Single Pole, Double Throw)] - 48:[Load voltage 480VAC] - 40:[40A]
Control Voltage:
85~265VAC (such as 100VAC, 110VAC/120VAC, 200VAC, 220VAC/230VAC, 240VAC or customized control voltage)
Control Current:
Ultra low input current, ≤10mA
Load Voltage:
Single phase 24~480VAC (such as 24VAC, 48VAC, 110VAC, 230VAC, 380VAC, 480VAC or customized load voltage)
Load Current:
10A, 15A, 20A, 25A, 30A, 40A
Dimensions & Mounting:
57.4mm*44.8mm*28mm; Panel mount solid state relay with transport cover,metal base and screw terminals
3.2 Why choose MGR (HUIMULTD)
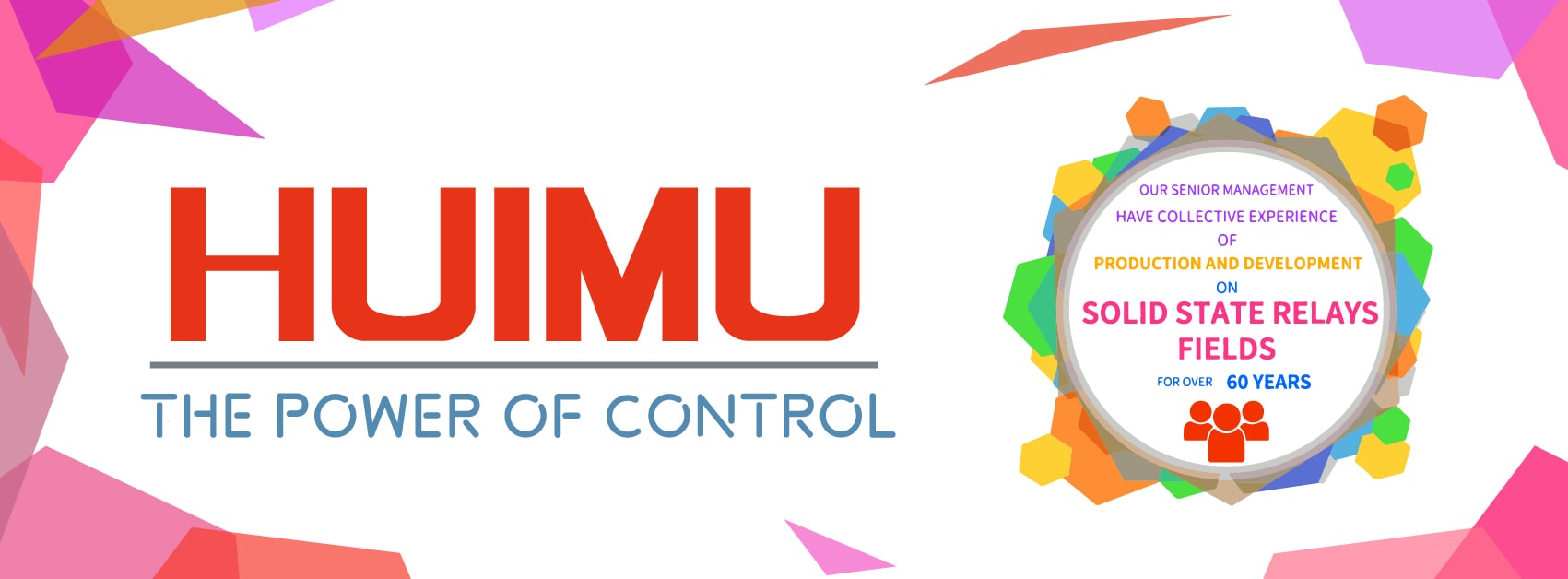
HUIMU Industrial specializes in providing industrial control products (such as Solid State Relays) and solutions, and consists of two companies: HUIMU Trade and MGR.
MGR is a modern high-tech company integrating R&D, manufacture, sales and service of solid state relays. Since its establishment, MGR has always been adhering to the purpose of " Innovation, Quality, Integrity", and the mission of "Manufacturing the High-Quality Industrial Control Products". For more than 20 years, MGR has continuously innovated and applied for a number of patents, and the MGR brand Solid State Relays are well sold at home and abroad.
MGR's full range of MGR solid state relays are available in a wide range of models and specifications, for example: single/three-phase solid state relay, voltage regulator, power regulator, DC motor governor, three-phase phase-shifting trigger (module), power electronic components (module), and so on. The wide product lines meet the needs of solid state relays in different industries; the high quality makes MGR solid state relays popular in all provinces and cities in China, as well as in Southeast Asia, the Middle East, Europe and the United States, and gains the trust of customers.
The Focus and Passion of technology, has enabled MGR to gather a number of senior engineers and professional technicians. With the joint efforts of the technical team, MGR 's research and development capabilities continue to improve and follow the times, and make it easy to design and develop OEM & ODM customized products according to customer needs.
The Perseverance and Pursuit in quality, make MGR demand itself with international standards. Each operation process strictly follows the IS09001 standard, each part is rigorously tested by superb testing equipment, and the experienced high-quality staff with team spirit is in harmony with advanced production equipment, and the purpose is only for manufacturing high-quality solid state relays.
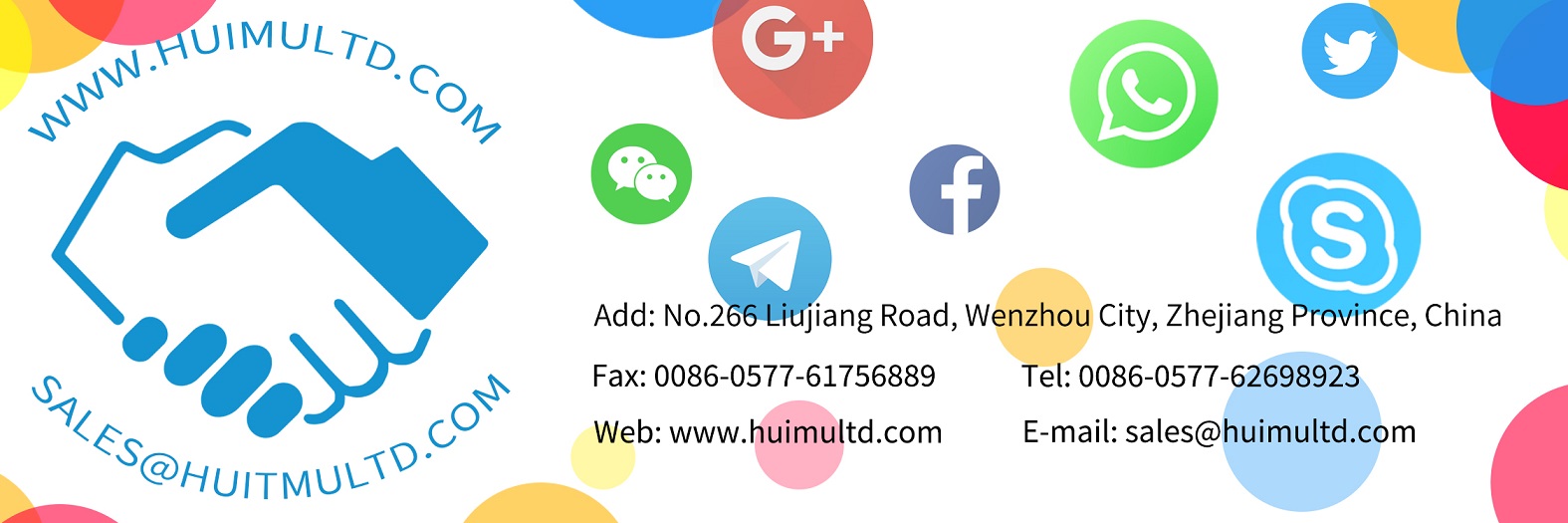
SPDT Solid State Relay - 2.WHAT IS SPDT SOLID STATE RELAY
§2. What is SPDT Solid State Relay
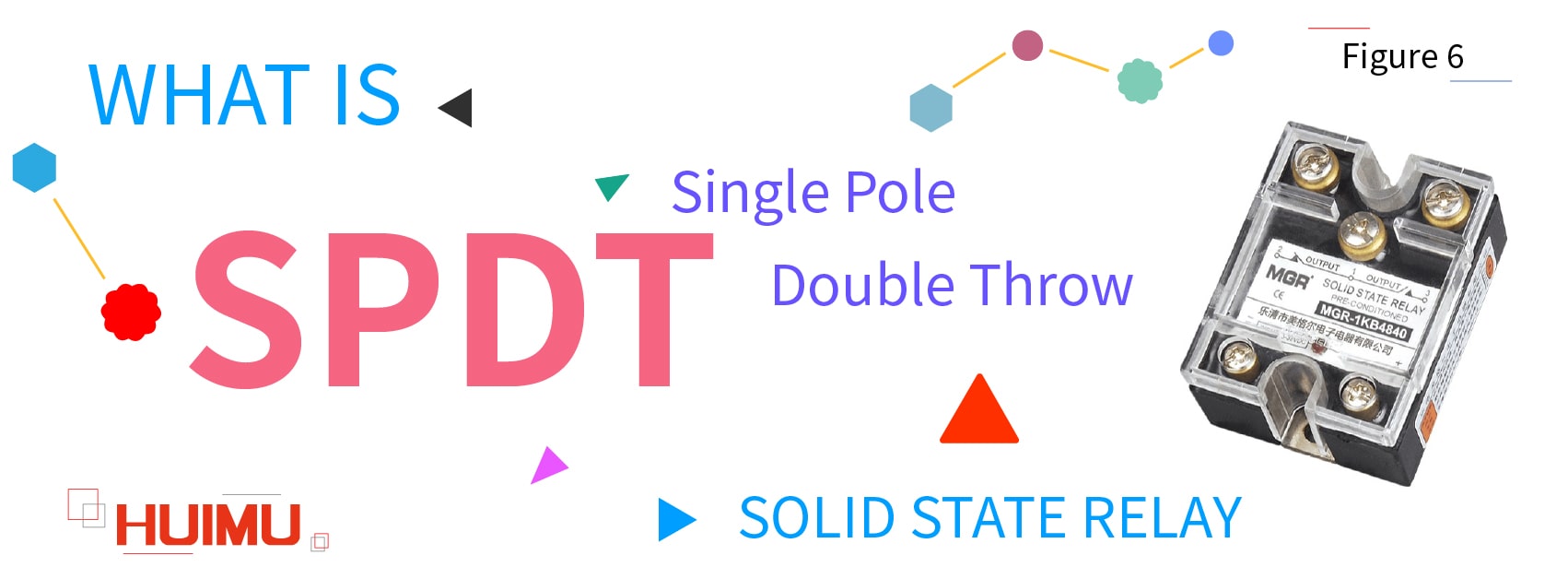
All the switch component (MOSFET, SCR, TRIAC, IGBT, etc.) in the solid state relay only acts as a SPST switch, and there is no single component in the solid state relay that has the SPDT function. Besides, the opto-coupler (with optoelectronic isolation feature) is used in the normal solid state relay as the signal transmission component, so the input control circuit of the SSR switch is electrical insulated to its output circuit. Therefore, if an SPDT solid state relay is required, we can only modify the SPST SSR switch by using a special circuit. And because of the electronic switch components, SPDT solid state relays is more efficient and consumes lower power than SPDT mechanical relays.
The basics of the SPDT SSR switch structure is a little different to the SPDT switch structure:
"Pole" – "Throw (Throw A and Throw B)":
"General-Purpose Push-Pull Outputs (GPout) ①" – "Diodes and Photodiodes";
"Photodiode array ②" – "N-channel enhancement mode MOSFET and N-channel depletion mode MOSFET"
Open: If the pole is disconnected to one throw, the state of this throw is called open state or open.
Close: If the pole is connected to one throw, the state of this throw is called close state or close.
NO (Normally Open): If the throw circuit is disconnected to the pole by default (when the pole is not energized or charged or the voltage level on the pole is zero), this throw circuit will be called the normally open circuit (NO circuit, N/O circuit), and the solid state relay switch will be called normally open SSR switch (NO SSR switch, N/O SSR switch).
NC (Normally Close): If the throw circuit is connected to the pole by default (when the pole is not energized or charged or the voltage level on the pole is zero), this throw circuit will be called the normally closed circuit (NC circuit, N/C circuit), and the solid state relay switch will be called normally closed SSR switch (NC SSR switch, N/C SSR switch).
① Push-Pull Outputs: The push-pull outputs are usually used for two triodes which are controlled by two complementary signals (that is, if one transistor is turned on, the other transistor must be turned off). And the push-pull outputs can output the high voltage level and low voltage level, both of which have the capability to drive the switch components.
② Photodiode array: the stack of photodiodes is used to drive a pair of MOSFETs or an IGBT.
2.1 How does SPDT Solid State Relay work
According to “Pole – Throw”, SPDT solid state relays can be divided into two types: Push-Pull type, and Photodiode-Array type.
1) Push-Pull Type SPDT Solid State Relay
The common circuit diagram of the push-pull SPDT SSR relay as shown below (as shown in Figure 7). The push-pull type SPDT SSR switch consists of two LEDs (D1, D2), and two Photo-TRIACs (TRIAC1, TRIAC2). D1 and TRIAC1 form the CIRCUIT1, and D2 and TRIAC2 form the CIRCUIT2. The push-pull signal (GPout) is generated in the input control terminal of the SPDT SSR, and LOAD1 and LOAD2 is connected to the two output terminals of the SPDT SSR relay.
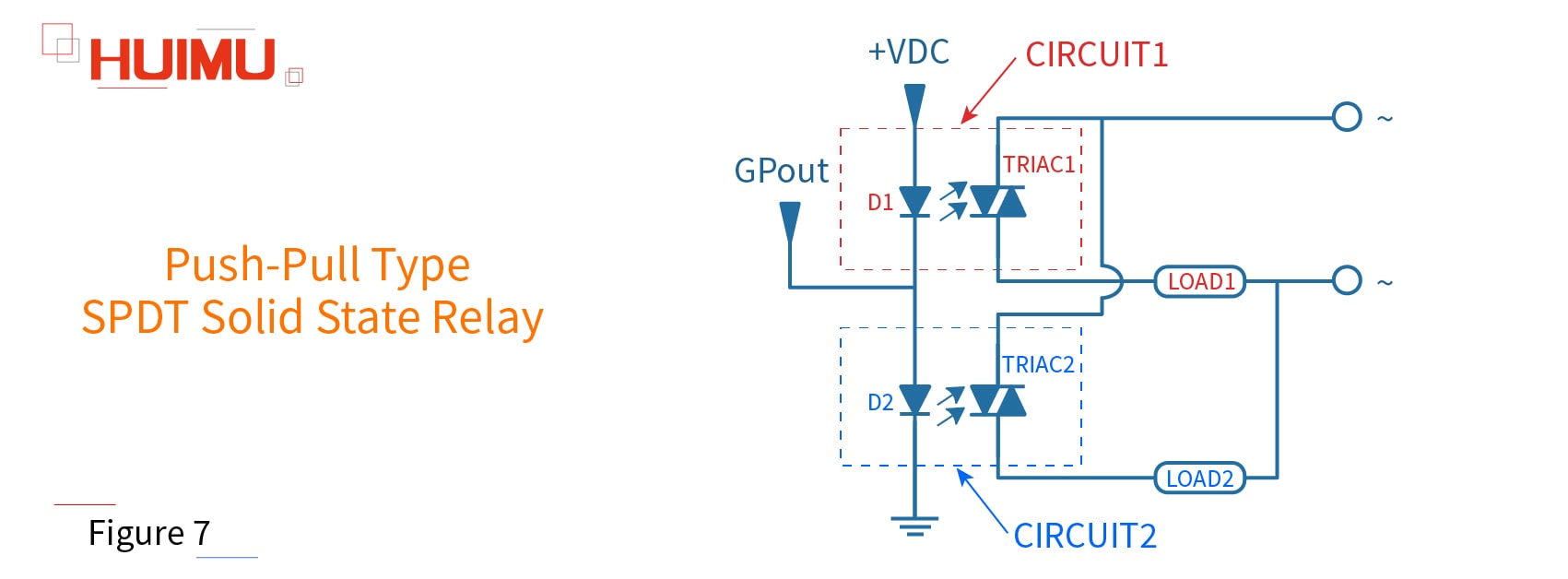
According to the GPout signal, there will be three status of the SPDT solid state relay:
1. When a low voltage level is generated in the input terminal, D2 will be turned off, and D1 will be turned on, and TRIAC1 will conduct, then the CIRCUIT1 will be closed, finally the LOAD1 will be switched on.
2. When a high voltage level is generated in the input terminal, D1 will be turned off, and D2 will be turned on, and TRIAC2 will conduct, then the CIRCUIT2 will be closed, finally the LOAD2 will be switched on.
3. If there is no signal on the input terminal, D1 and D2 will be turned off, and CIRCUIT1 and CIRCUIT2 will not be switched on.
Note: Since the GPout outputs and the operating voltage of LED needs to meet certain limits and requirements, the application of Push-pull type SPDT solid state relay is not very extensive.
2) Photodiode-Array Type SPDT Solid State Relay
Following shows the common circuit diagram of the photodiode-array SPDT SSR relay (as shown in Figure 8), which can work in DC power supply and AC power supply. The photodiode-array type SPDT SSR switch consists of one photodiode-array (D1), and four N-MOSFETs (MOS1 and MOS2 are enhancement mode N-MOSFETs③; MOS3 and MOS4 are depletion mode N-MOSFETs④). MOS1 and MOS2 form the CIRCUIT1, and MOS3 and MOS4 form the CIRCUIT2. There are 5 output terminals, Port1, Port2, Port3, Port4, Port5, and the Port1 is the common terminal. LOAD1 and LOAD2 is connected to the SPDT switch.
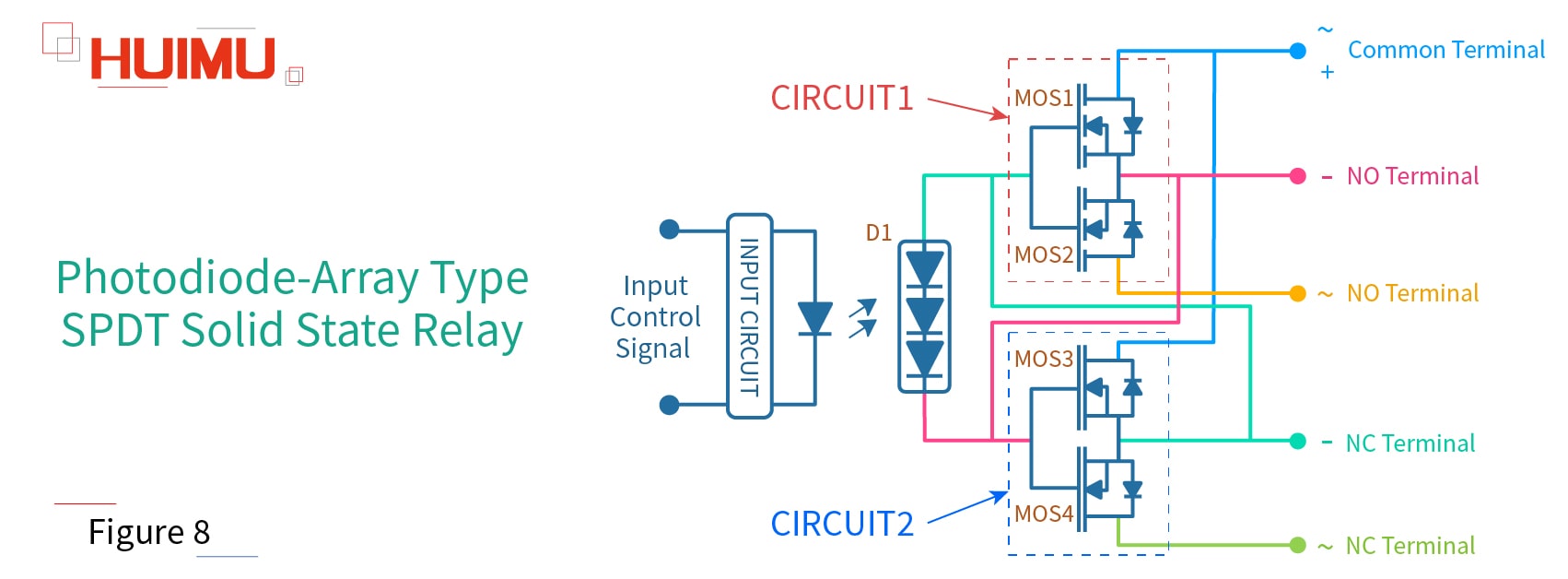
③ The enhancement mode N-channel MOSFET will turn on when Vgs>Vgs(th)⑤, otherwise it will not conduct.
④ The depletion mode N-channel MOSFET will turn on at zero input, and turn off when its Vgs is negative.
⑤ Vgs is the voltage from gate to source; Vgs(th) is the threshold voltage from gate to source.
1. DC Power Supply
When the photodiode-array SPDT SSR relay is working in a DC power supply, the LOAD1 should be connected to the PORT2, and the LOAD2 should be connected to the PORT4, so the MOS2 and MOS4 will not work.
When photodiode array is disabled, the gate voltage of the MOS1 is below its threshold voltage and won't turn on, so the LOAD1 is switched off; the gate voltage of the MOS3 is zero input and will conduct, so the LOAD2 will be switched on (as shown in Figure 9).
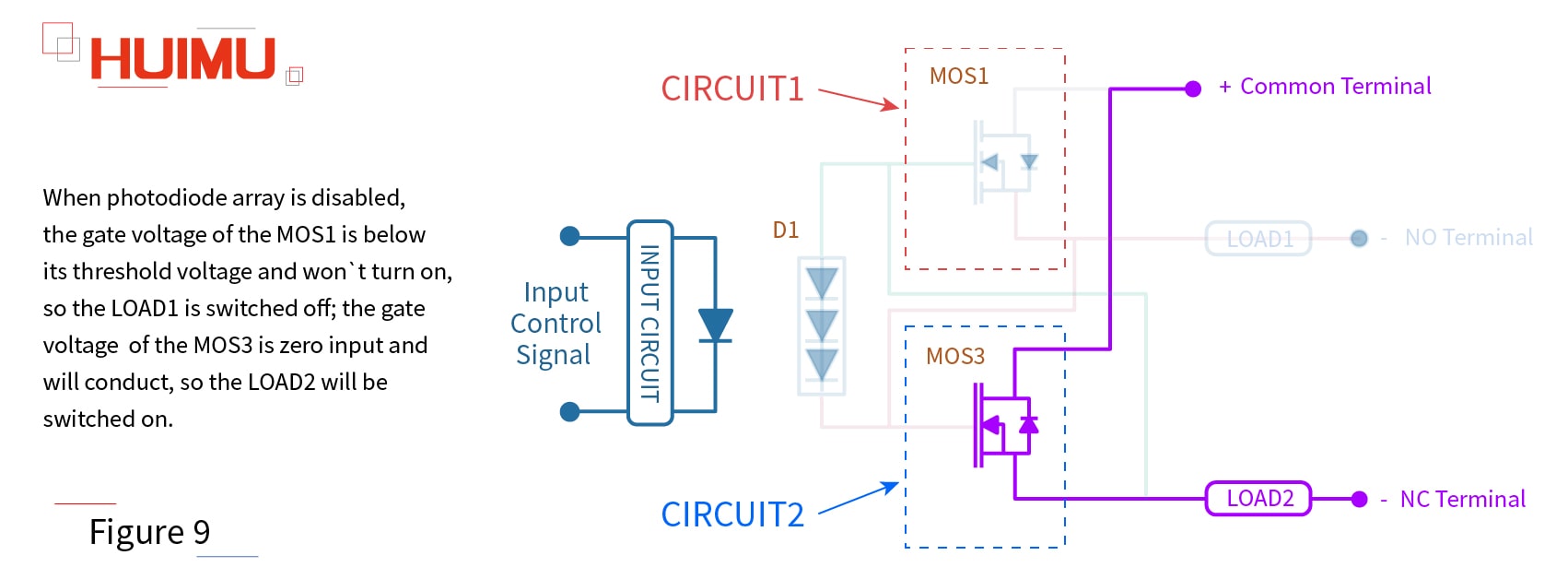
When photodiode array is enabled, the gate voltage of the MOS1 is above its threshold voltage and be turned on, so the LOAD1 will be switched on; the gate voltage of the MOS3 is negative and will not conduct, so the LOAD2 will be switched off (as shown in Figure 10).
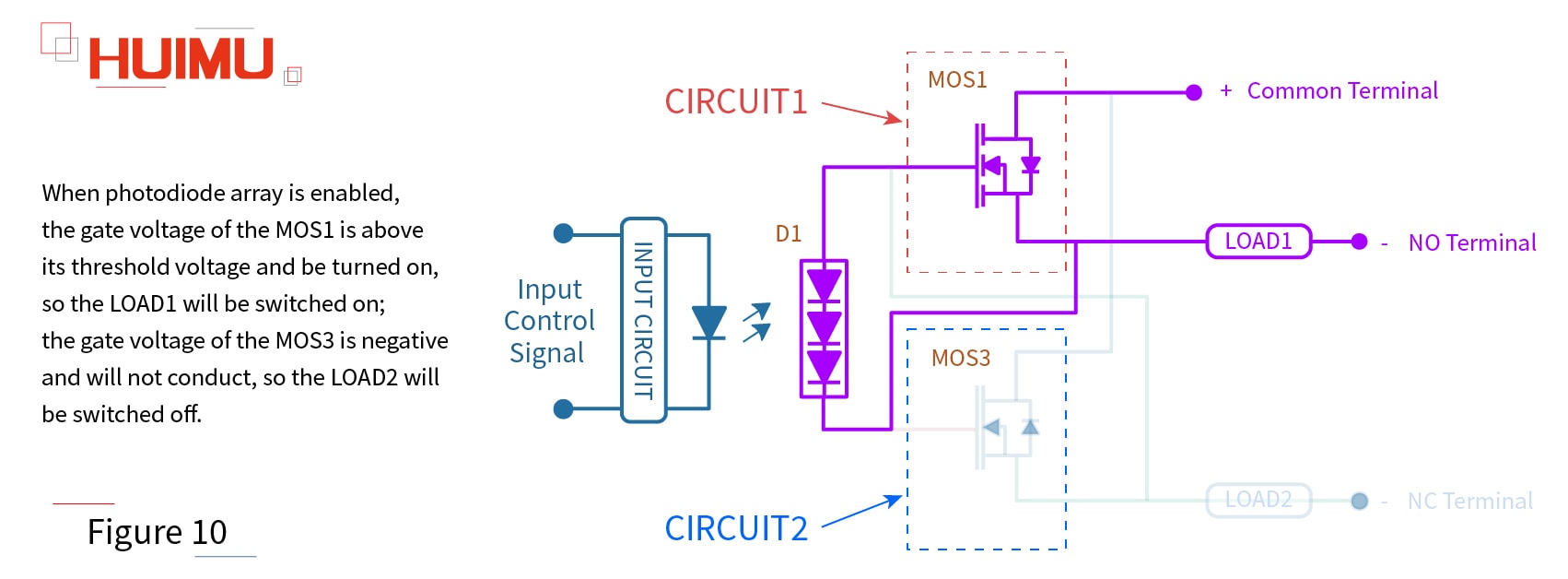
2. AC Power Supply
When the photodiode-array SPDT SSR relay is working in an AC power supply, the LOAD1 should be connected to the PORT3, and the LOAD2 should be connected to the PORT5.
When photodiode array is disabled, the gate voltage of the MOS1 and MOS2 is below its threshold voltage and won't turn on, so the LOAD1 is switched off; the gate voltage of the MOS3 and MOS4 is zero input and will conduct, so the LOAD2 will be switched on (as shown in Figure 11).
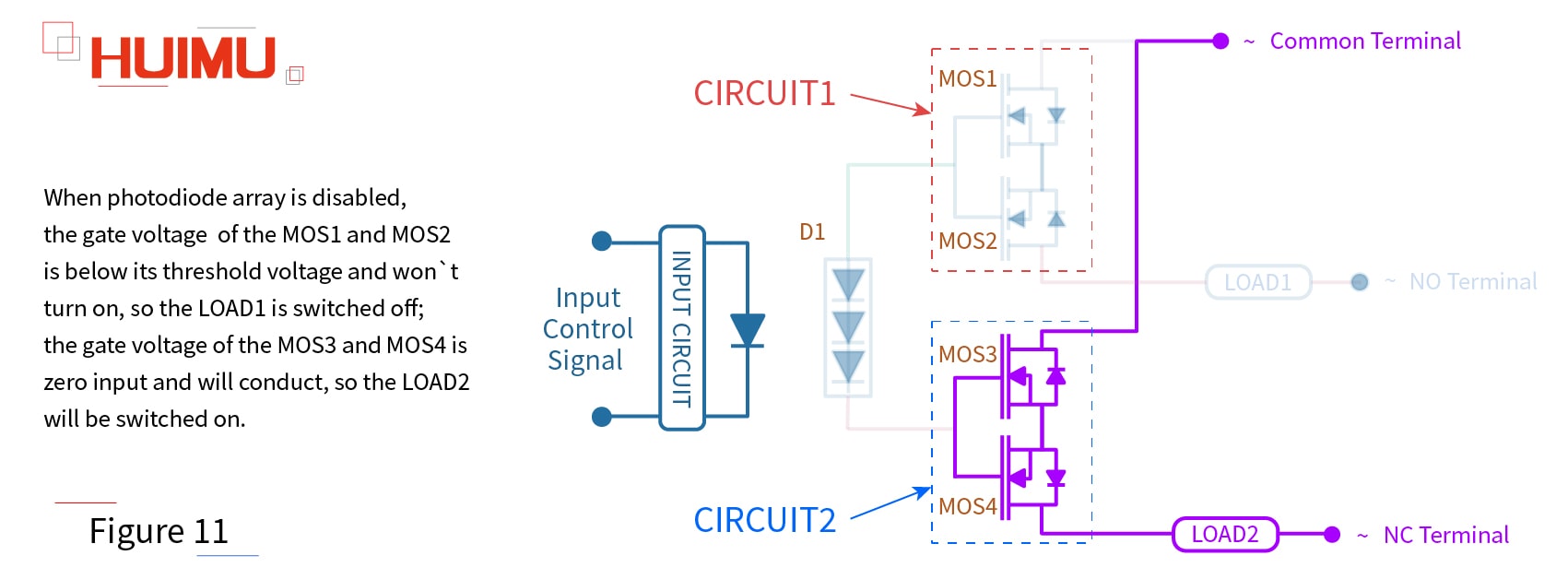
When photodiode array is enabled, the gate voltage of the MOS1 and MOS2 is above its threshold voltage and be turned on, so the LOAD1 will be switched on; the gate voltage of the MOS3 and MOS4 is negative and will not conduct, so the LOAD2 will be switched off (as shown in Figure 12).
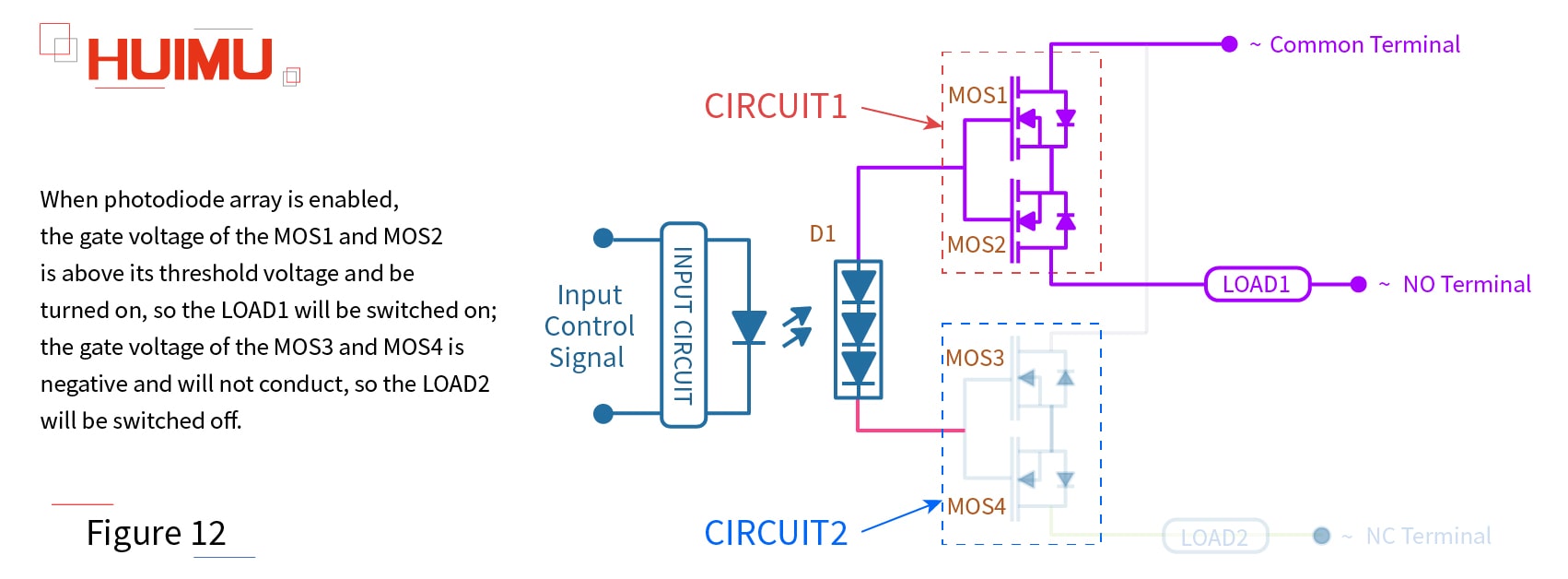
Note: Because of the features of N channel enhancement MOSFETs and N channel depletion MOSFETs, this kind of solid state relays are widely used to control the DC load circuit and the AC load circuit.
2.2 What is SPDT solid state relay used for
Solar Battery Charger
SPDT solid state relays are typically used in solar power charger systems (such as portable solar charger) to control the solar cell charging equipment. The working state (charging state and power state) of the solar cells is switched much frequently, so the SPDT mechanical relays cannot meet this requirement, but the SPDT SSRs can.
Soft Starter System
When the electronic/electrical systems (and their subsystems) works normally, the switching frequency of its soft start state and stop state is very high. Therefore, the SPDT make-before-break switch need to be equipped to prevent overvoltage when switching.
Remote Control Device / Radio Transmitter
If the remote control device wants to control multiple objects, it needs to change the transmitted signal; if the communication tower wants to switch the recipient, it needs to change the transmission signal. This kind of equipment require strict operating frequency and operation accuracy, and SPDT solid state relays can meet these requirements in most cases.
Satellite Heater
In the space environment, there are high requirements (weight, anti-interference ability, adaptability, and so on) to every device. The SPDT solid-state relay (with lots of advantages, like small weight, high performance, long service life, low power consumption, low EMR and etc.) meet these requirements, and is much better than the SPDT electromechanical relay (simple structure, but high weight, poor anti-interference ability and cannot adapt to complicated situations due to overweight).
SPDT Solid State Relay - 1.WHAT IS SPDT SWITCH
§1. What is SPDT Switch
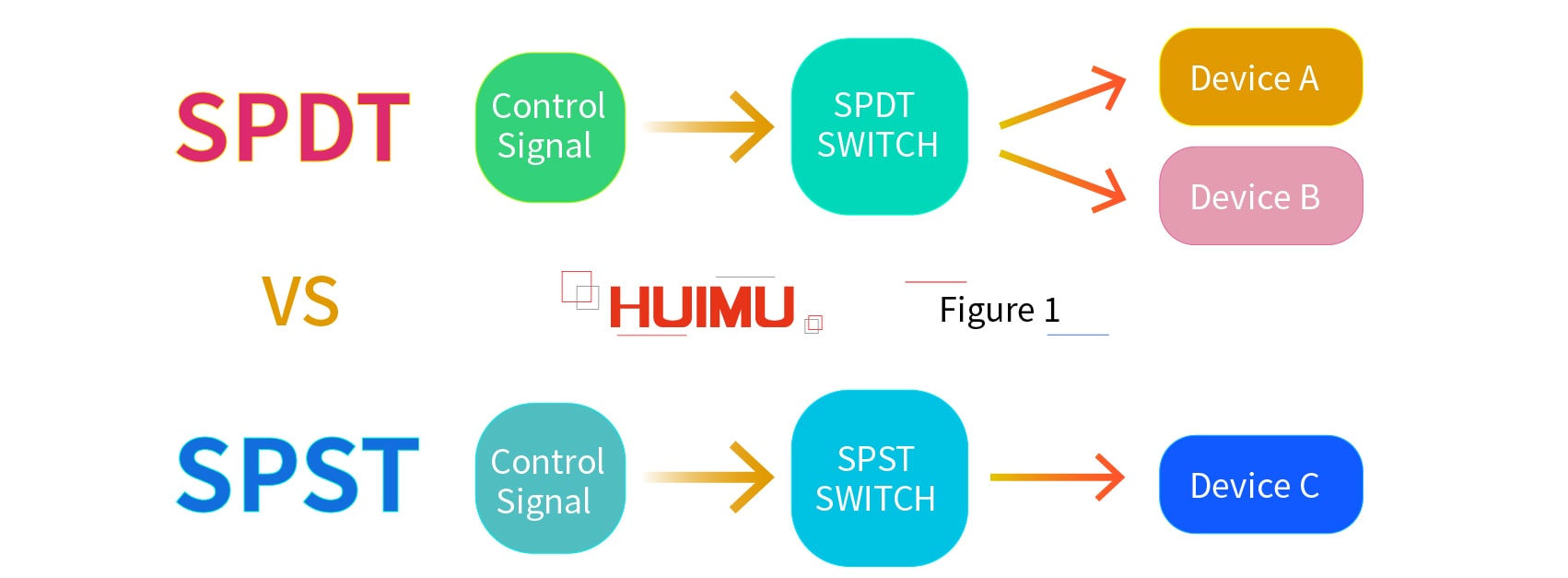
SPDT (Single Pole Double Throw) is a special switch structure. Different with the normal SPST (Single Pole Single Throw) switches, SPDT switches control the working status of two devices, and these two devices work in opposite status. For example, a SPDT switch is connected to Device A and Device B, the Device A will be on status and the Device B is shut down if the SPDT switch is switched off; conversely, if the SPDT switch is switched on, the Device A will be off status and the Device B will be turned on. Therefore, we can know that no matter what state the SPDT switch works on, only one device will be turned on.
1.1 What is the Structure of SPDT Switch
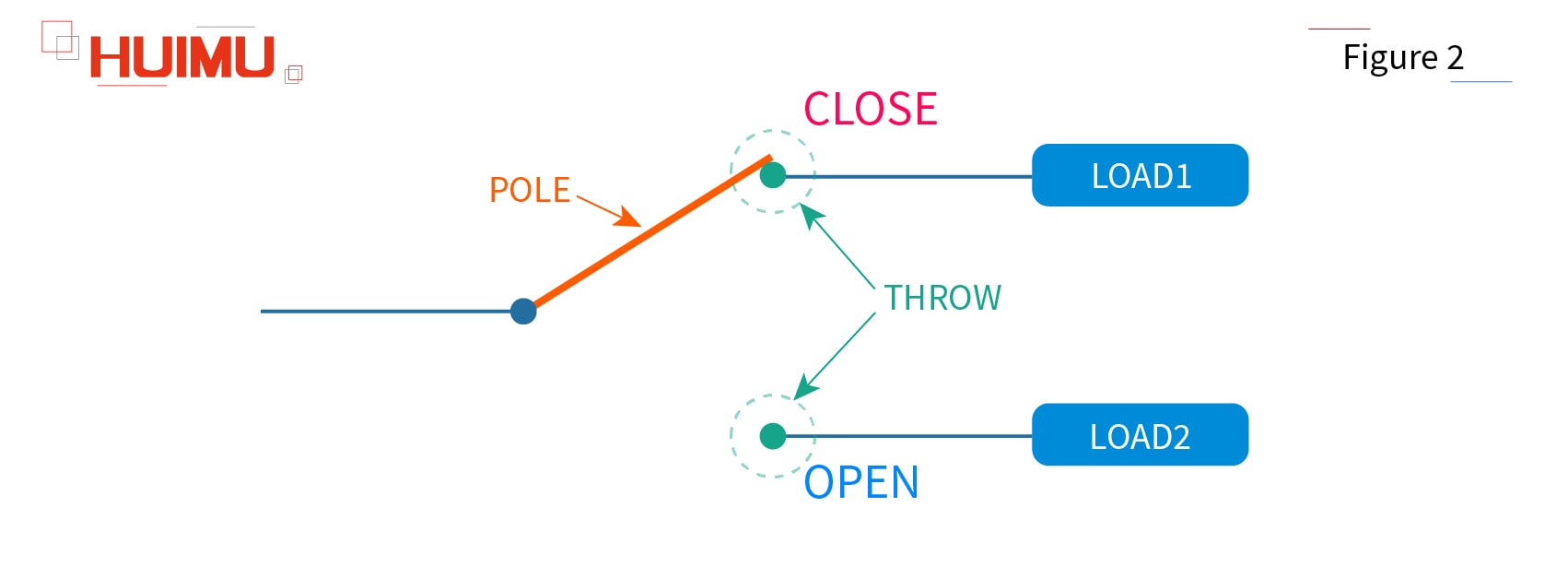
The basics of the SPDT switch structure:
Pole: The pole is the controller inside the switch. We usually use single pole, double pole, or etc. to show how many separate circuits that controlled by the switch.
Throw: The throw means the circuit that will be controlled by the pole. We usually use single throw, double throw, or etc. to show how many circuits will be controlled by one Pole.
Open: If the pole is disconnected to one throw, the state of this throw is called open state or open.
Close: If the pole is connected to one throw, the state of this throw is called close state or close.
NO (Normally Open): If the throw circuit is disconnected to the pole by default (when the pole is not subject to any external forces), this throw circuit will be called the normally open circuit (NO circuit, N/O circuit), and the switch will be called normally open switch (NO switch, N/O switch).
NC (Normally Close): If the throw circuit is connected to the pole by default (when the pole is not subject to any external forces), this throw circuit will be called the normally closed circuit (NC circuit, N/C circuit), and the switch will be called normally closed switch (NC switch, N/C switch).
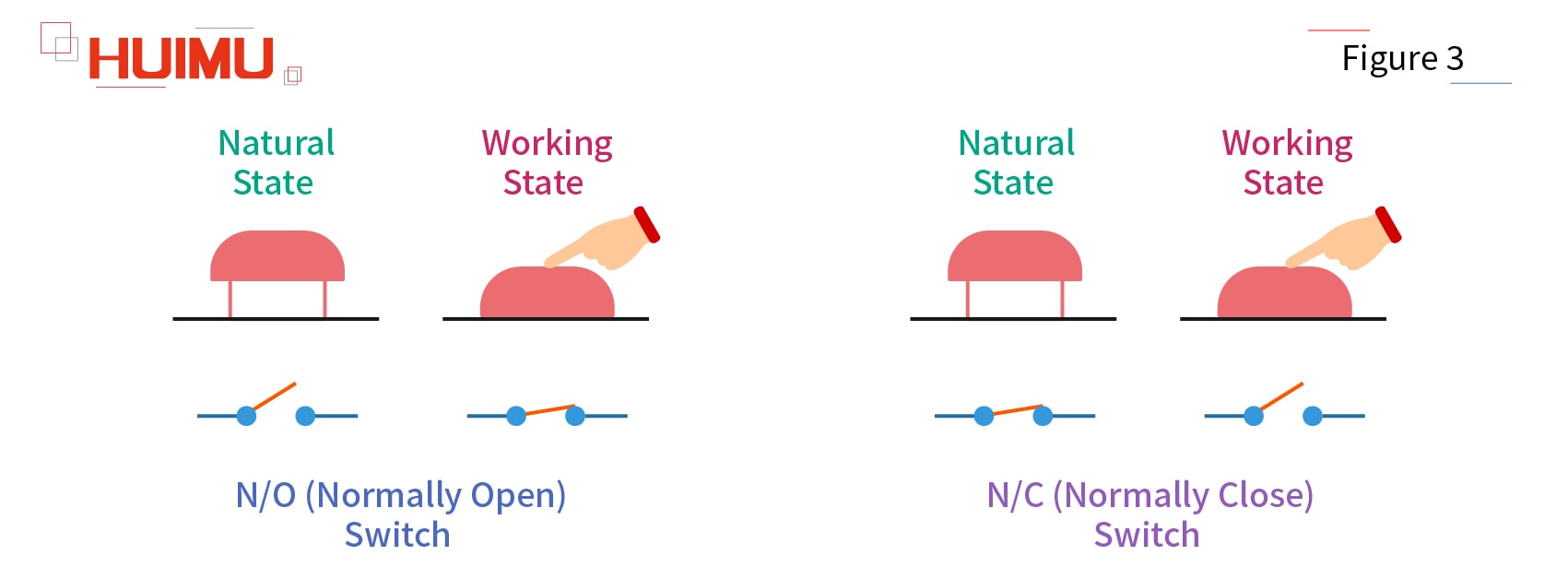
SPDT switch is a five terminal switch device — two input terminals, and three output terminals (two terminals connect to the load, and one terminal connect to the common terminal). And if one of SPDT switch output terminals does not connect to any circuit (which means only one control circuit and one output circuit are connected to the SPDT switch), the SPDT switch functions as a SPST switch.
Generally, the SPDT switch will be more suitable and efficient for some special applications than what two normal SPST switches (which need two control circuits) can do, like switching two different power supplies in opposite status, or activating two circuits with different functions in opposite status.
1.2 How does SPDT Switch work
According to the way of operating, the single pole double throw switch can be divided into BBM type SPDT switch (break-before-make) and MBB type SPDT switch (make-before-break).
1) BBM (Break Before Make) SPDT Switch
By default, the pole of the BBM SPDT switch is connected to NC throw circuit and disconnected from the NO throw circuit. When the break-before-make switch is switched, it will first disconnect to the NC circuit, and then connect to the NO circuit.
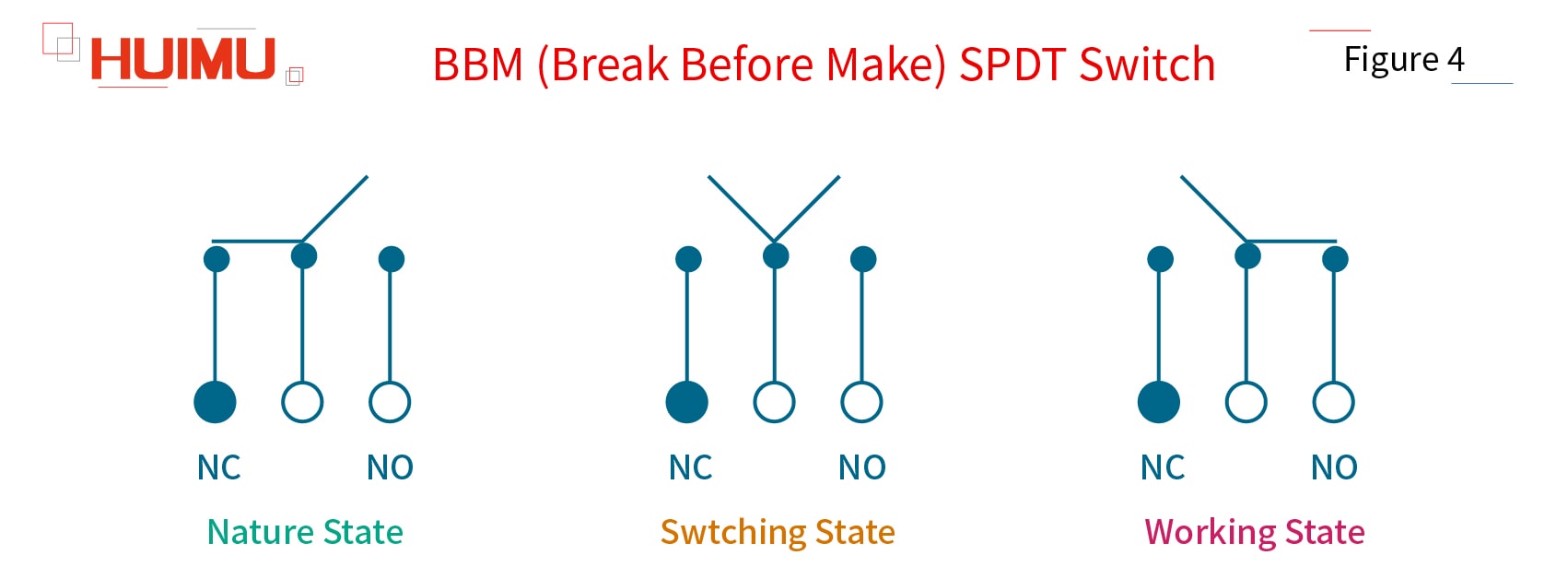
2) MBB (Make Before Break) SPDT Switch
By default, the pole of the MBB SPDT switch is connected to NC throw circuit and disconnected from the NO throw circuit. When the make-before-break switch is switched, it will first connect to the NO circuit, and then disconnect to the NC circuit.
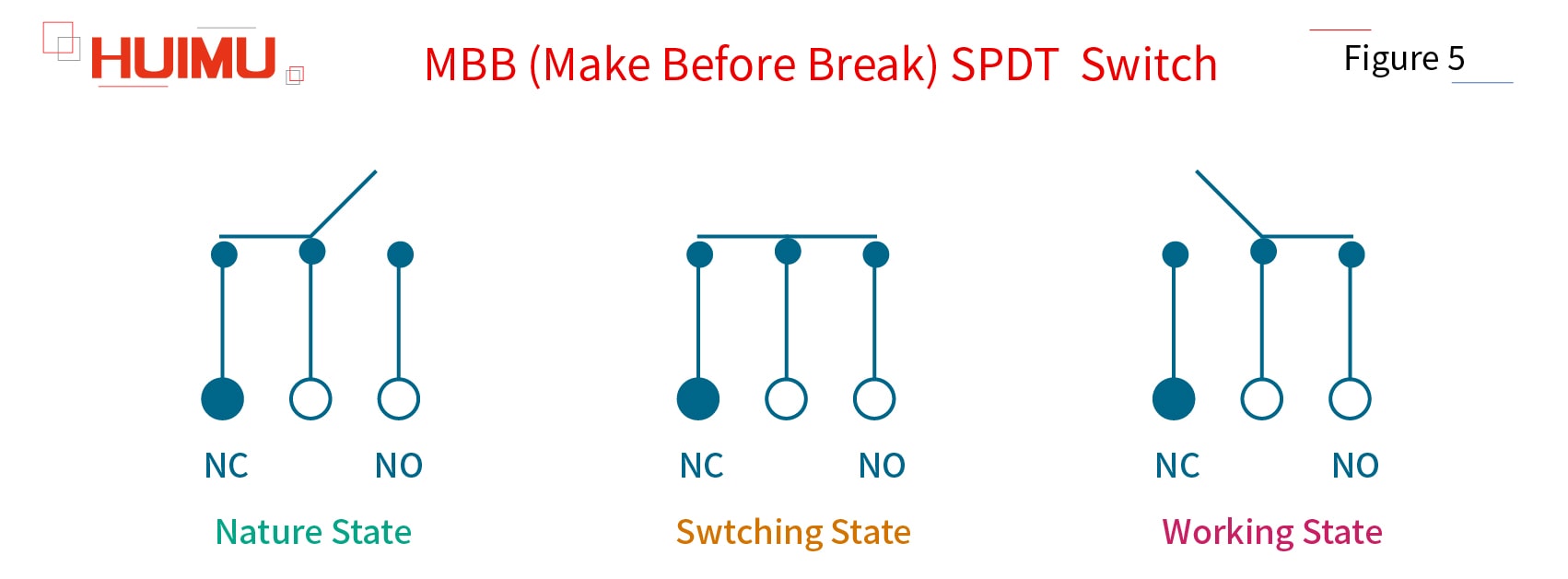
How To Order SSR
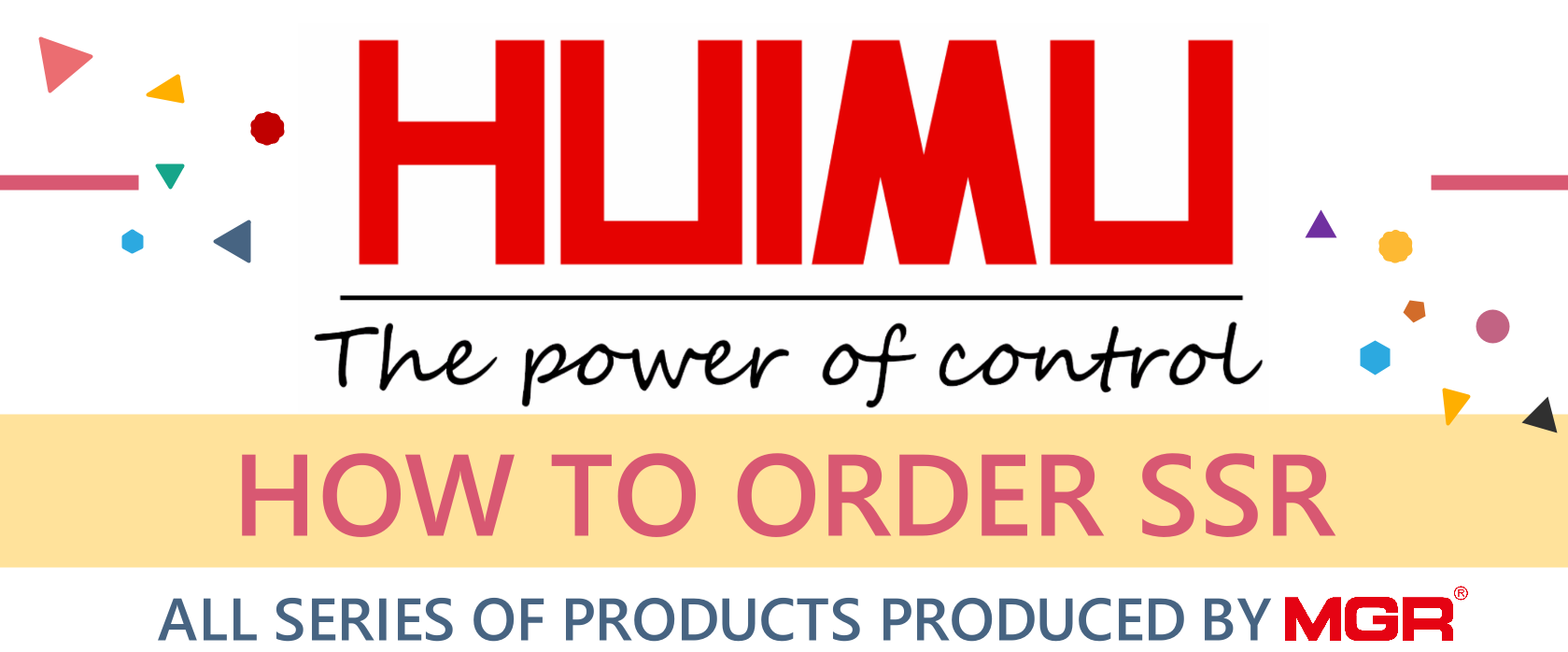
How to select a suitable heat sink for solid state relays and solid state modules?
§1. How the Heat Sink works
The role of the heat sink is to dissipate the heat generated by the solid state relay or module to ensure that the solid state relay or module will work stably and reliable at optimum conditions and not be burned and damaged due to high temperatures. The heat dissipation effect of the heat sink is not only related to its specification (size, shape), but also related to external environmental factors, such as the ambient temperature (season), ventilation conditions (natural cooling or forced cooling, and ventilation volume), and installation density. In addition, it is also necessary to consider whether the volume of the solid state relay or the module itself and the installation space of the heat sink in the equipment matches the specifications of the heat sink.
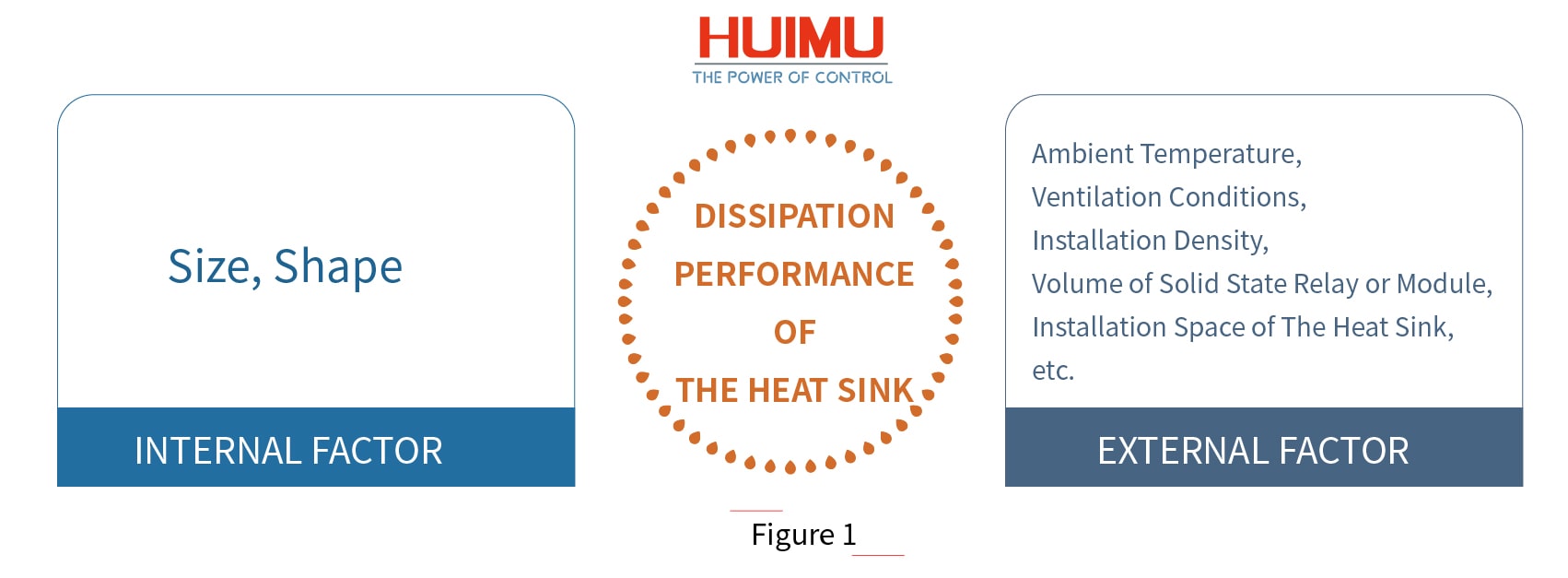
The cooling method of the solid state relay/module can be divided into Air Cooling method and Water Cooling method. And the air cooling heat sink can be farther divided into the Heat Sink (natural cooling) and Air Cooled Radiator (forced cooling by fan). Normally, if the load current of the solid state relay/module reaches 10A, a heat sink must be equipped; if the load current is 40A or more, an air-cooled radiator or a water-cooled radiator must be installed. When the module is used for the load with load power greater than 15 KW, it is recommended to use a suitable heat sink, and apply thermal grease between the heat sink and the SCR backplane, as well as cold air to cool down. If the current is below 350A, the module is cooled by forced air cooling; if the current is more than 400A, the cooling method for the module can be either air-cooling or water-cooling.
Heat dissipation reference standard: The temperature of the bottom plate (the side in contact with the heat sink) of the solid state relay or module does not exceed 80 °C.
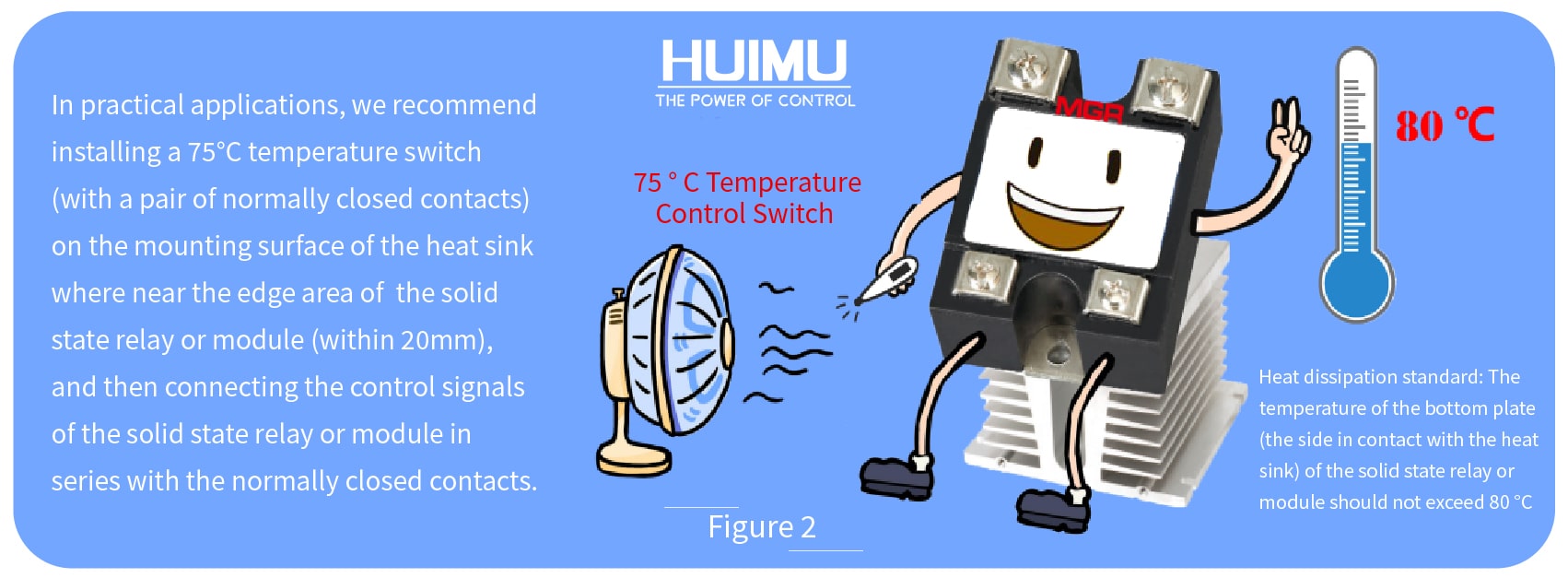
In practical applications, we recommend installing a 75°C temperature switch (with a pair of normally closed contacts) on the mounting surface of the heat sink where near the edge area of the solid state relay or module (within 20mm), and then connecting the control signals of the solid state relay or module in series with the normally closed contacts. In this way, when the temperature of the detection point exceeds 75 °C, the normally closed contact will trip and cut off the control signal, and the output terminal of the solid state relay or module will be forcibly turned off to get protection. Generally, if the solid state relay or module is installed to the place with the actual current of each phase exceeding 50A, the high installation density and ambient temperature, it is better to apply a temperature switch for protection to ensure that the temperature of the bottom plate of the solid state relay or module does not exceed 80 ° C under severe conditions.
§2. How to calculate the Heat
At first, we should know that there is no one-to-one correspondence between the model (type) of the heat sink and the model (type) of the solid state relay or module. Since solid-state relays use transistors as electronic switching components/power components, the heat generated by the solid state relay or module is mainly related to the actual current of the load it drives, instead of its own rated current specification (current grade).
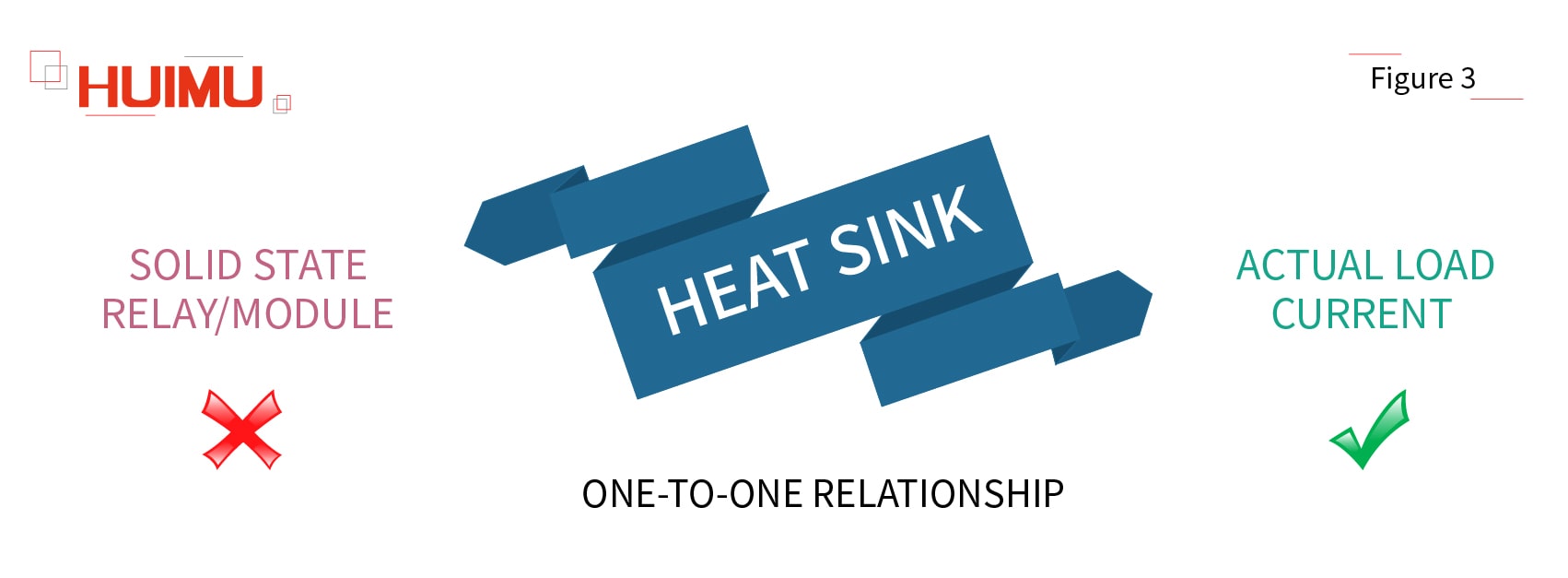
The heat generated by the solid state relay/module in practical applications can be calculated by the following formula:
1. Heat = Actual Load Current (Amps) * 1.5 W/Amps
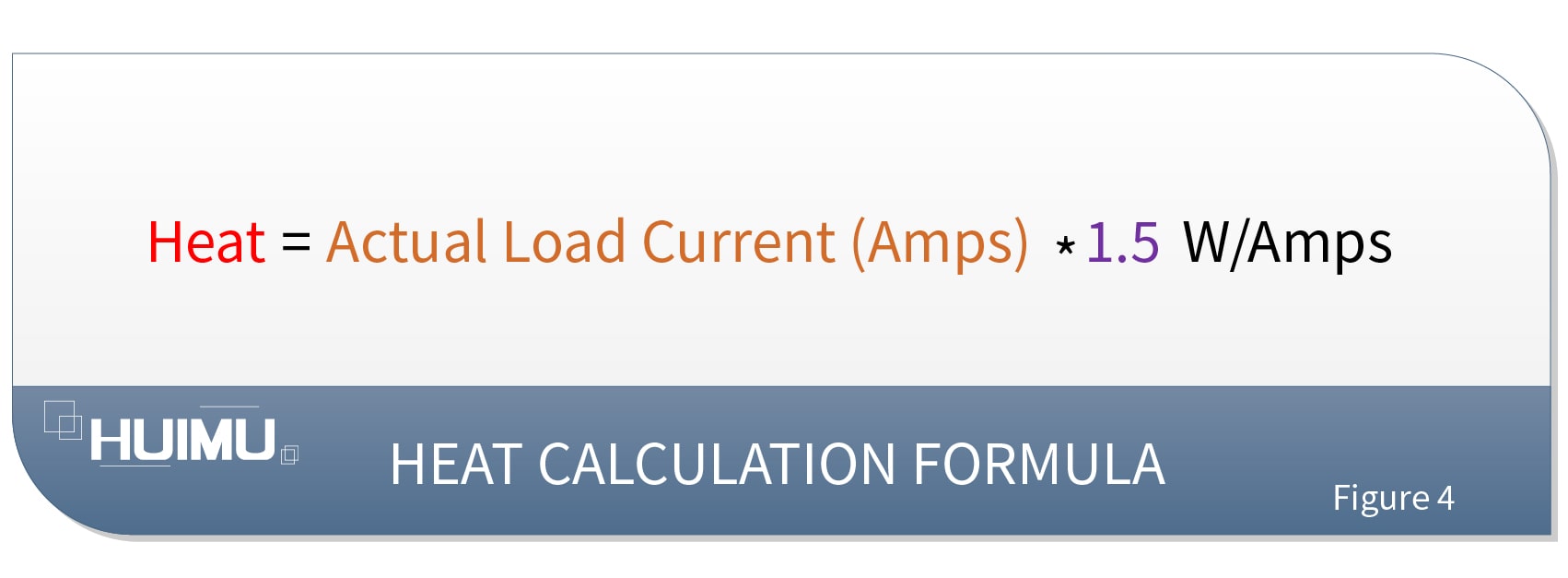
Note: The above formula is suitable for single phase solid state relays, single phase AC voltage regulator modules, and R series solid state voltage regulators. For three phase solid state relays and three phase AC voltage regulator modules, the actual load current should be the sum of the actual load currents.
2. Heat = Actual Load Current (Amps) * 3.0 W/Amps
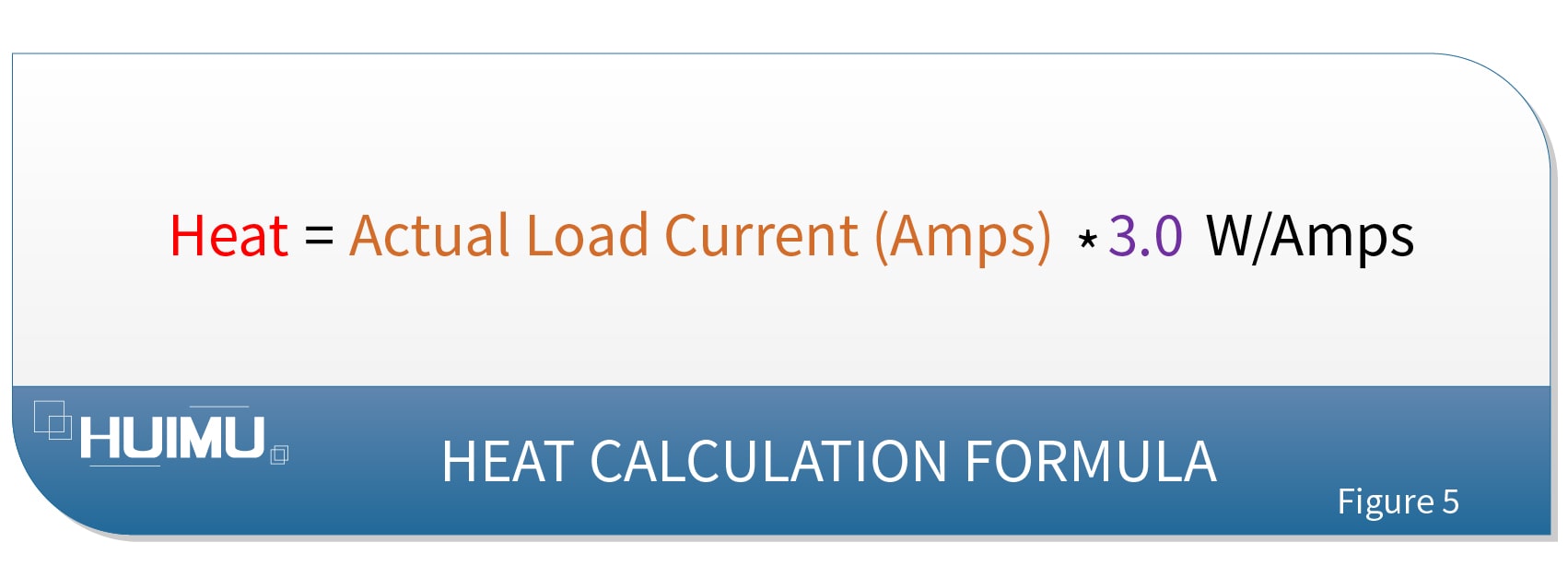
Note: The above formula is suitable for single phase fully-controlled bridge rectifier module.
§3. How to select Heat Sink / Radiator
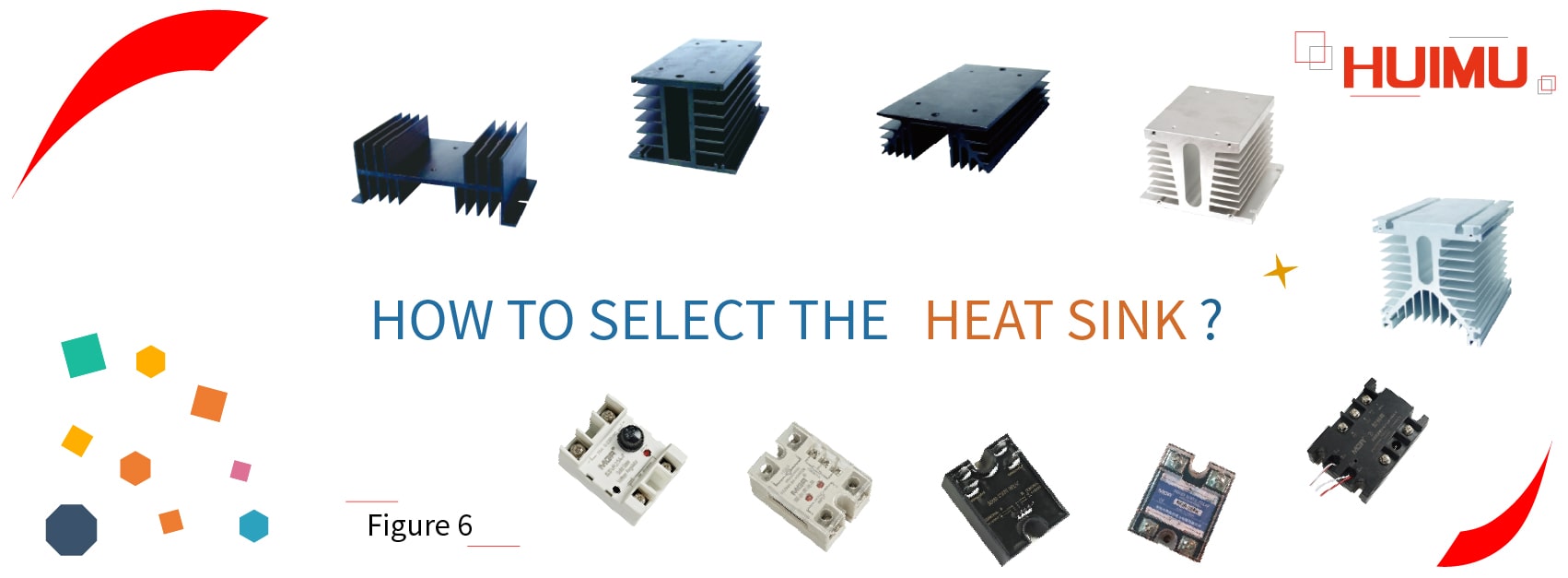
MGR (HUIMULTD) Heat Sink / Radiator series
The heat sinks/ radiators produced by our company are divided into two categories, for solid state relay and for module.
◆ For Solid State Relay: MG-I, MG-W, MG-T, MG-L, MG-H, MG-F, MG-Y.
These seven series are suitable for a variety of single phase solid state relays, single phase AC voltage regulator modules, R series solid state voltage regulators, industrial solid state relays and various three phase AC solid state relays, etc.
◆ For Module: E series, K series, Z series, Y series, G series.
These series are usually used with an air-cooled fan, suitable for DC commutator modules, voltage regulator modules, rectifier modules, phase-shift trigger modules, thyristor modules, hybrid modules, welding machine modules, etc.
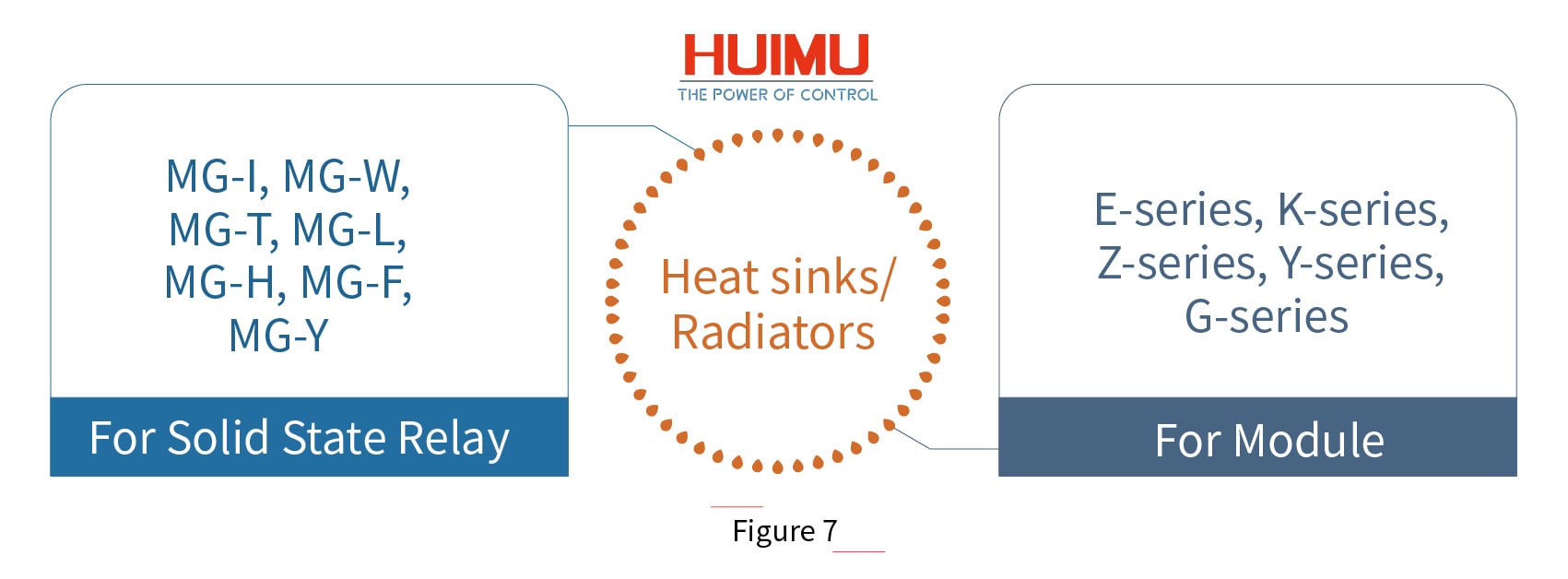
The following are the general applications and selection of some radiators:
MGR-DT Series Full Isolation Single Phase AC Solid State Voltage Regulator Module
The heat of the whole module = Actual load current (Amps) * 1.5 W/Amps. Customers can select MG-L, MG-H series heat sink according to actual needs.
MGR-DQZ Series Single Phase Full Isolation Fully-Controlled Solid State Bridge Rectifier Module
The heat of the whole module = Actual load current (Amps) * 3.0 W/Amps. Customers can select MG-L, MG-H series heat sink according to actual needs.
MGR-STY Series Full Isolation Three Phase AC Voltage Solid State Voltage Regulator Module
The heat of the whole module = Actual load current (Amps) * 1.5 W/Amps. Customers can select MG-Y, MG-H series heat sink according to actual needs.
SSR-3JK Series Three Phase Solid State Phase-Shift Trigger Module (For Solid State Relays)
SSR-3JK and TB-3 generate very little heat and do not need to be mounted on a heat sink.
The SSR-3JK (with TB-3) matches the random solid state relays produced by our company. Users can build the SSR-3JK system by purchasing the SSR-3JK, the TB-3, three random conduction type SSRs and one heat sink to. If three long strip solid state relays are selected, they can be mounted on a Y series module air-cooled radiator with a fan installed to form a power unit; and if three rectangular solid state relays are selected, they can be mounted on the MG-Y heat sink to form a power unit.
SX-JK Series Three Phase Solid State Phase-Shift Trigger Module (For Thyristor Circuits)
SX-JKA, SX-JKT, SX-JKZ, SX-JKB, TB-3A, and TB-3Z generate very little heat and do not need to be mounted on a heat sink.
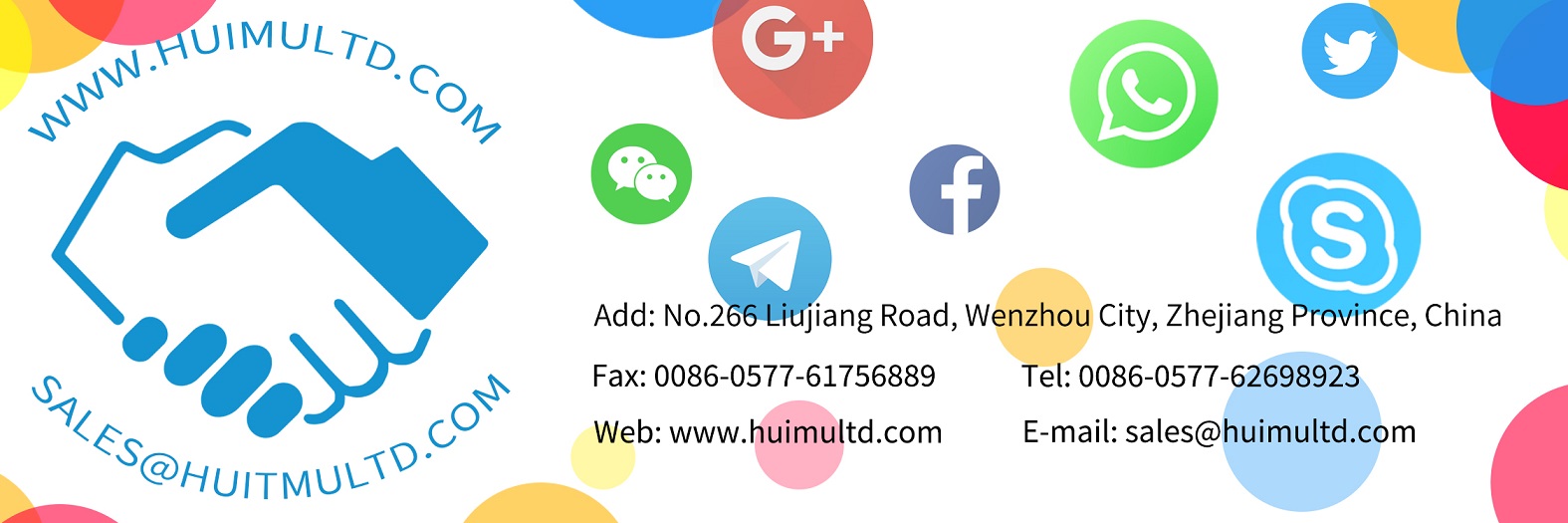
Relays-Comparation - 2.WHY CHOOSE SOLID STATE RELAYS
§2. Why choose Solid State Relays
ADVANTAGES
Electromagnetic Relay | Solid State Relay |
AC and DC compatible | Anti-vibration, anti-shock |
Can provide multiple sets of contacts; normally open and normally closed contacts are both available | Anti-corrosion and moisture proof |
Cheap price | Asynchronous & synchronous switching mode |
Compact size | Compatible with digital circuits |
Low residual voltage | Fast response time |
No heat sink required | Low control power, usually 10-50 mW |
No leakage current | Long life, 50-100 times longer than electromagnetic relays |
Low electromagnetic interference(EMI) in synchronous switch mode | |
No mechanical strain | |
No mechanical moving parts | |
No noisy action |
DISADVANTAGES
Electromagnetic Relay | Solid State Relay |
Contact bounce | Leakage current |
High control power. Usually higher than 200mW | Not suitable for small output signals |
Limited contact life | Only a single contact |
Maximum switching frequency is limited (5-10mhz) | Output can only be AC or DC, not compatible |
Noisy action | Residual voltage 1-1.6V |
Need interface for the digital loop | Usually need a heat sink |
Poor working ability for large currents, will produce electric arc | |
Produce electromagnetic interference (EMI) during operation | |
Switch action cannot be fully synchronized |
The above table helps to compare the advantages and disadvantages of SSR and EMR, and it can be found that the characteristics of SSR and EMR are different due to different structures. However, in actual application, the advantages of solid state relay are very obvious, and due to the excellent advantages as follows, which is the reason why use solid state relays, and why Solid State Relays gradually replace the Electromechanical Relays in many fields.
1.Long-life and high stability
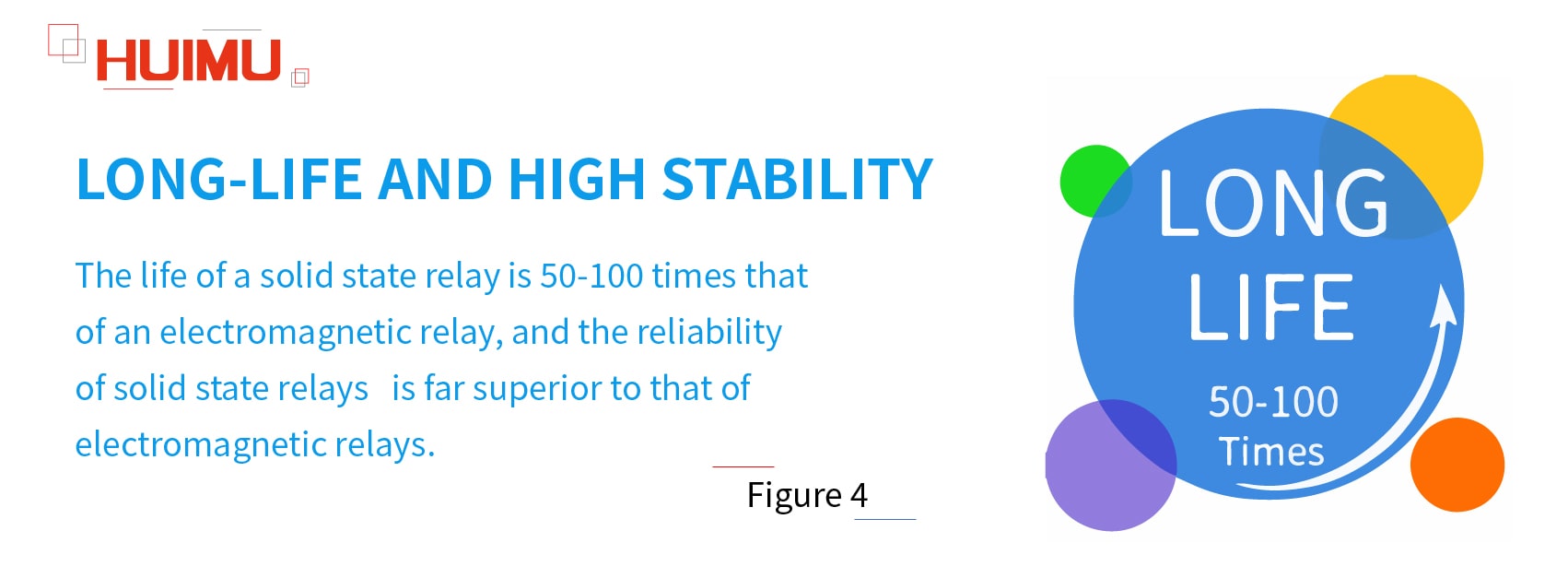
Actually, the life of the mechanical contacts determines the life of the mechanical relay. Since there are no mechanical contacts inside the solid state relay, the service life of the SSR relays will not be shortened due to the strain, aging, corrosion, and adhesion of the contacts. At the same time, there are no mechanical moving parts (such as springs, reeds) inside the solid state relay, so contact bounce and poor contact of moving parts will not occur.
Due to the non-contact structure and the resin shell protection, the solid state relays have good impact resistance, shock resistance and corrosion resistance. Solid state relays have a wider range of applications than EMR, for examples, the humidity has little effect on the solid state relay and only slightly reduces its insulation performance, but electromagnetic relays are very sensitive to humidity, if exposed to moisture for extended periods of time, the service life of the EMR will be shortened and components will be corroded.
In summary, the life of a solid state relay is 50-100 times that of an electromagnetic relay, and the reliability of solid state relays is far superior to that of electromagnetic relays.
2.Cost of use
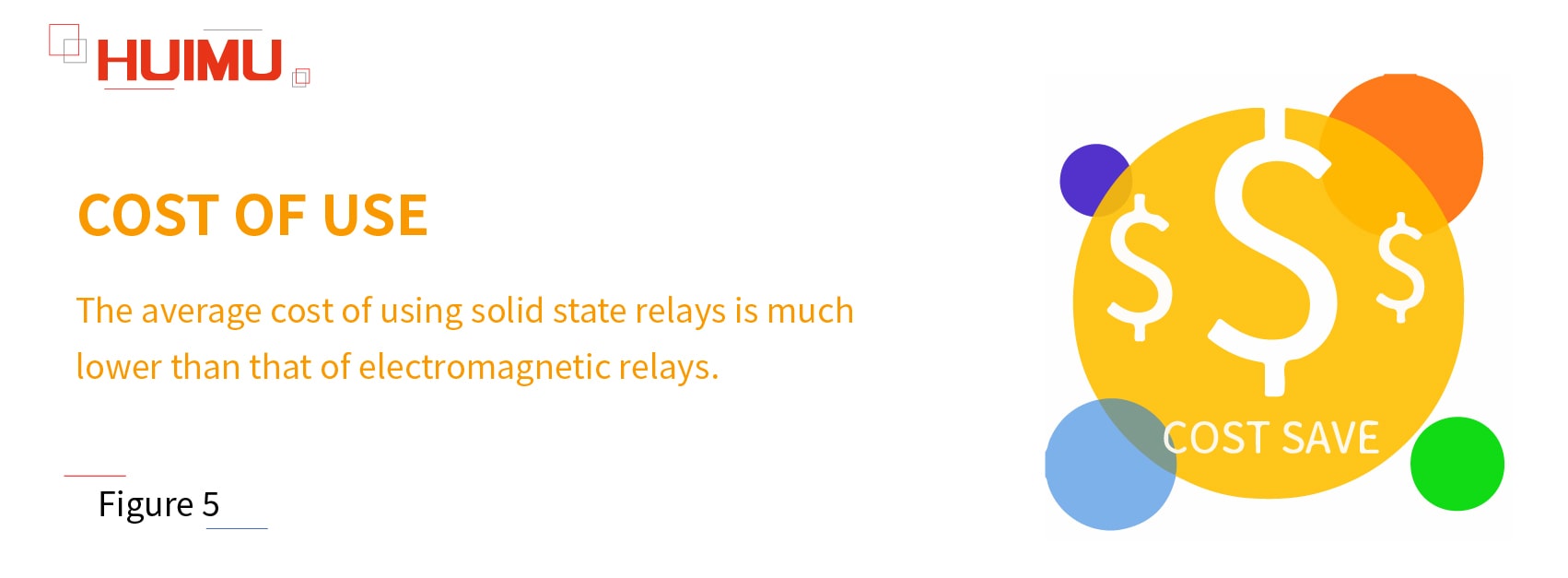
The initial purchase cost of solid state relays is higher than that of electromagnetic relays. But considering of other costs (like the comprehensive service life, the cost of inspection and maintenance, the loss and low efficiency due to the unstable or faulty of relays, and etc.), the average cost of using solid state relays is much lower than that of electromagnetic relays.
In addition, in some applications, additional costs are required to prevent contact vibration and poor contact of the mechanical relay.
3.Efficient control
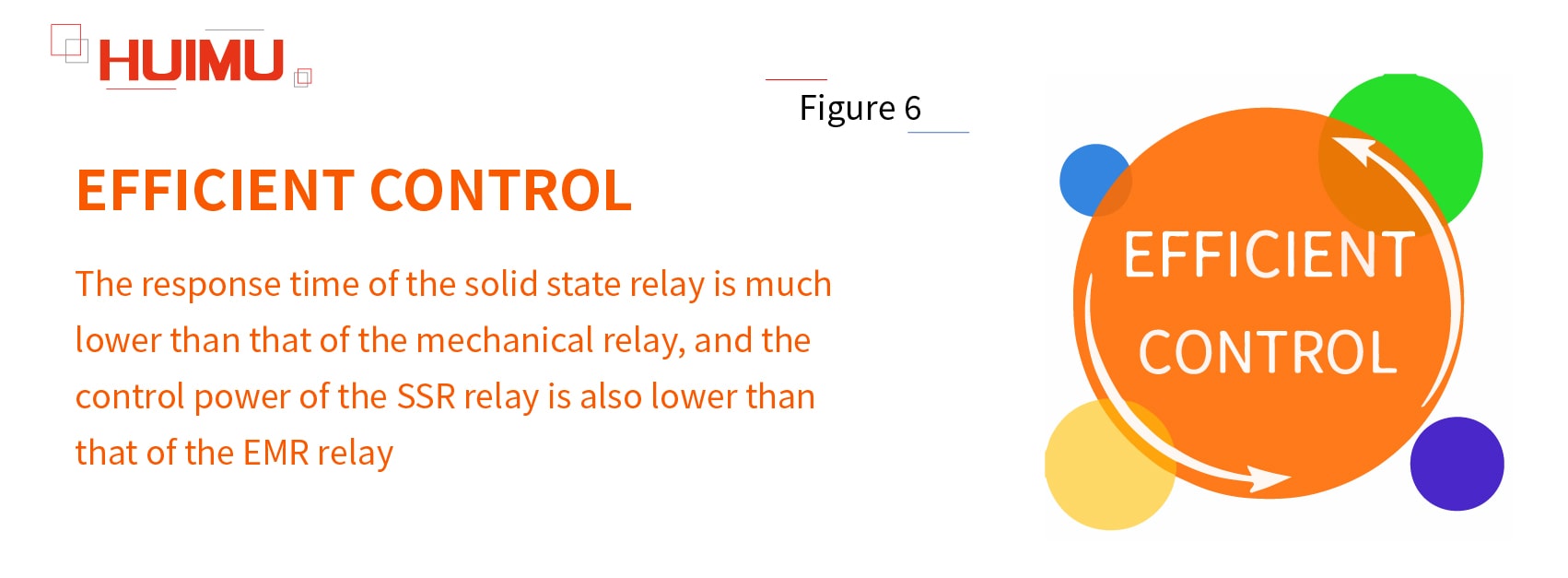
The operating frequency (or switching rate) of solid state relays is several to several tens of times that of electromagnetic relays, which enables SSRs to be used in equipment that requires high efficiency. Moreover, solid-state relays use semiconductors as signal transmission media, so solid-state relays can be compatible with computer control systems without adding additional circuits and equipment, but EMR cannot do it.
The response time of the solid state relay is much lower than that of the mechanical relay, and the control power of the SSR relay is also lower than that of the EMR relay, which makes the EMR not applicable to equipment that requires short response time and low control power. In some special applications that requires low power factor, the switch must be stable and not subject to vibration, so EMR relays cannot be used either.
4.Electromagnetic radiation
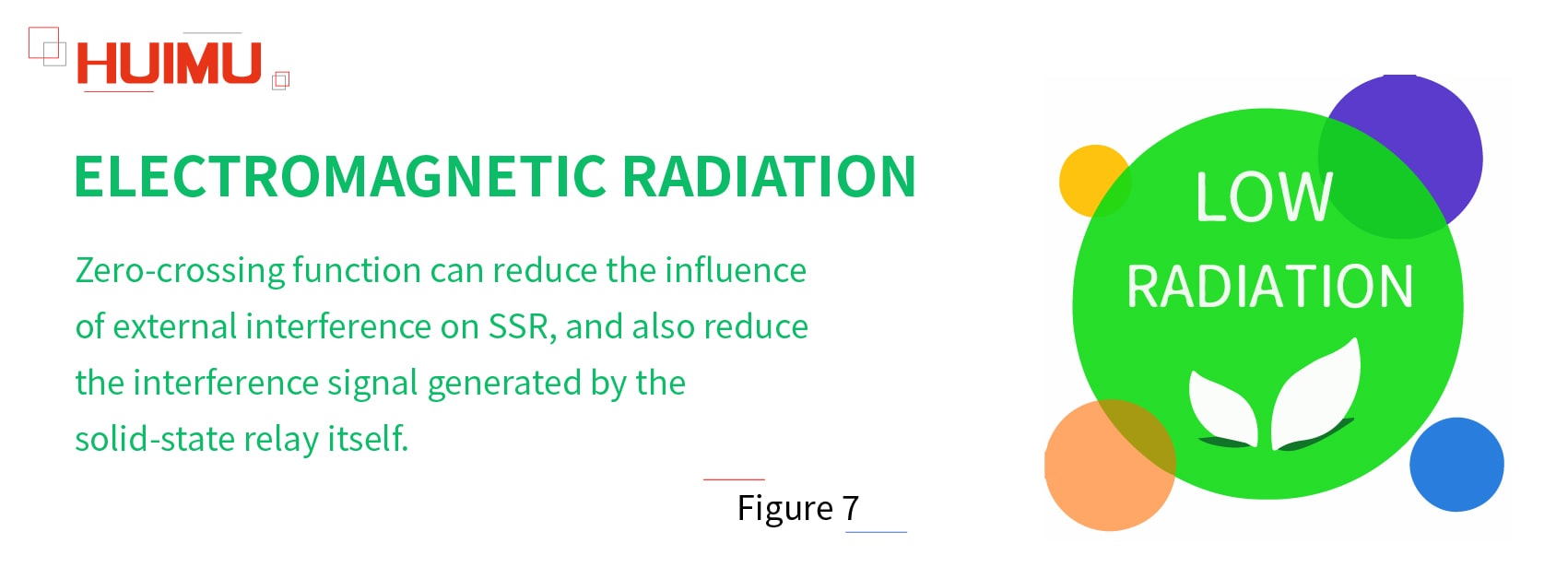
The mechanical structure causes the mechanical relay to generate a large amount of electromagnetic interference (EMI) signals during switching period. If there is no addition protection circuit, these interference signals may adversely affect the electronic device and the power grid. And strong electromagnetic interference will even damage the human body.
In contrast, the solid state relay has good electromagnetic compatibility (EMC). And the solid state relay with zero-crossing function can reduce the influence of external interference on SSR, and also reduce the interference signal generated by the solid-state relay itself.
Therefore, if the application requires low electromagnetic interference, only solid state relays recommended.
5.More action modes
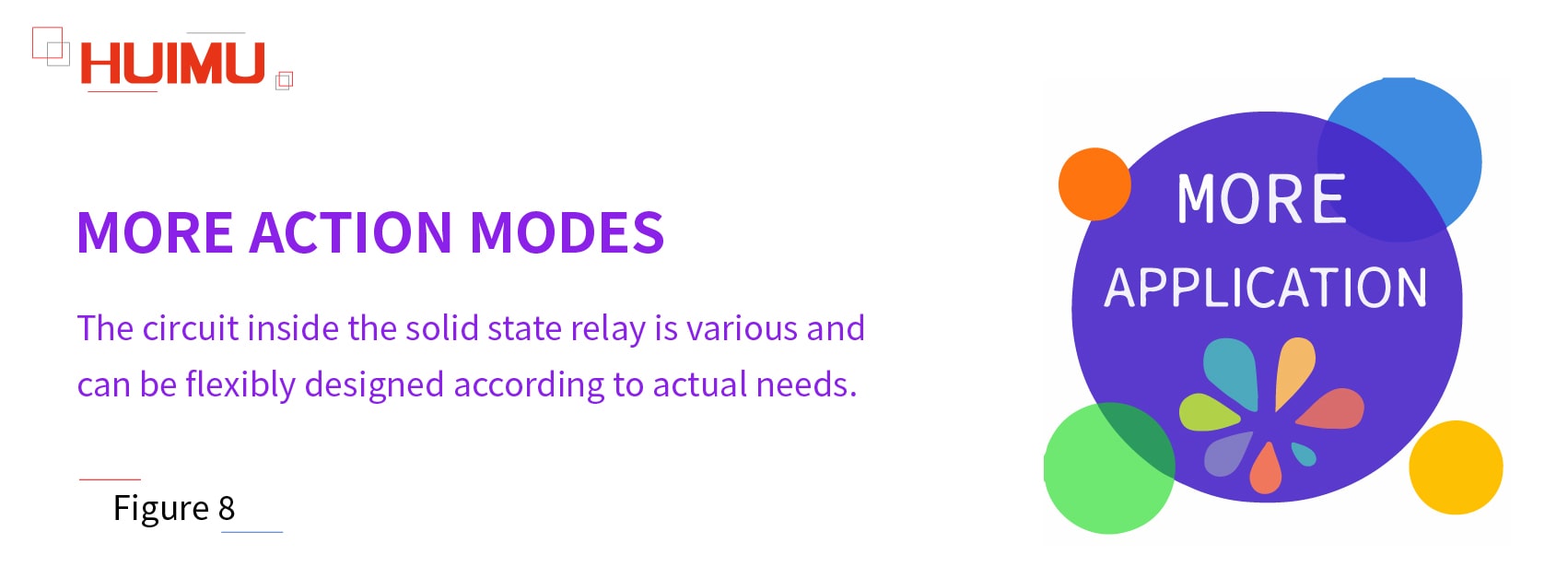
The circuit inside the solid state relay is various and can be flexibly designed according to actual needs. Through the combination of internal components, solid state relays can achieve a variety of control of the output circuit according to different state of control signals and power supplies.
However, electromagnetic relay can only switch the load asynchronously, that is to say, the state of the switch is only controlled by the control signal and is time-independent of the power signal; whereas the solid state relay can realize the control synchronously. Of course, solid state relays have more action modes, such as:
1)Asynchronous mode
2)Synchronous mode
3)Voltage zero or peak sync mode
4)Phase angle mode
5)Pulse mode
§3. Why choose HUIMU Industrial

HUIMU Industria is a company specializing in solid state relays, and supplies high-quality solid state relays and solutions to the world. Our Senior Management have collectively over 60 years` experience of production and development in Solid State Relay fields. And we are proud to offer high quality products and provide our customers with the services and support they deserve. According to customer needs, we can design solid state relays in different forms and specifications, and also provide deep OEM customized services to meet different requirements.
We strictly control the production and components of our products. Every component comes from excellent and reliable suppliers, each operation process strictly follows the IS09001 standard, and each part is rigorously tested by superb testing equipment. And products and components will be 100% tested before delivery to ensure that each manufactured product is delivered to the customer with optimal performance.
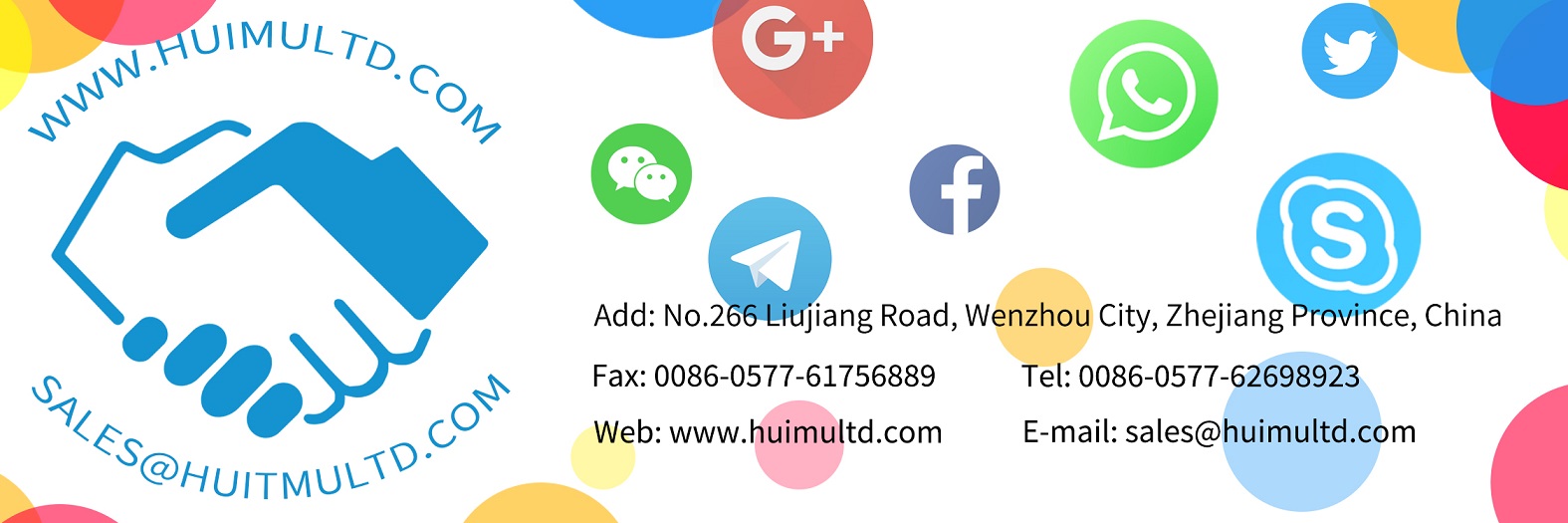
Relays-Comparation - 1.COMPARATION IN SSR AND EMR
§1. What are the Differences between SSR and EMR
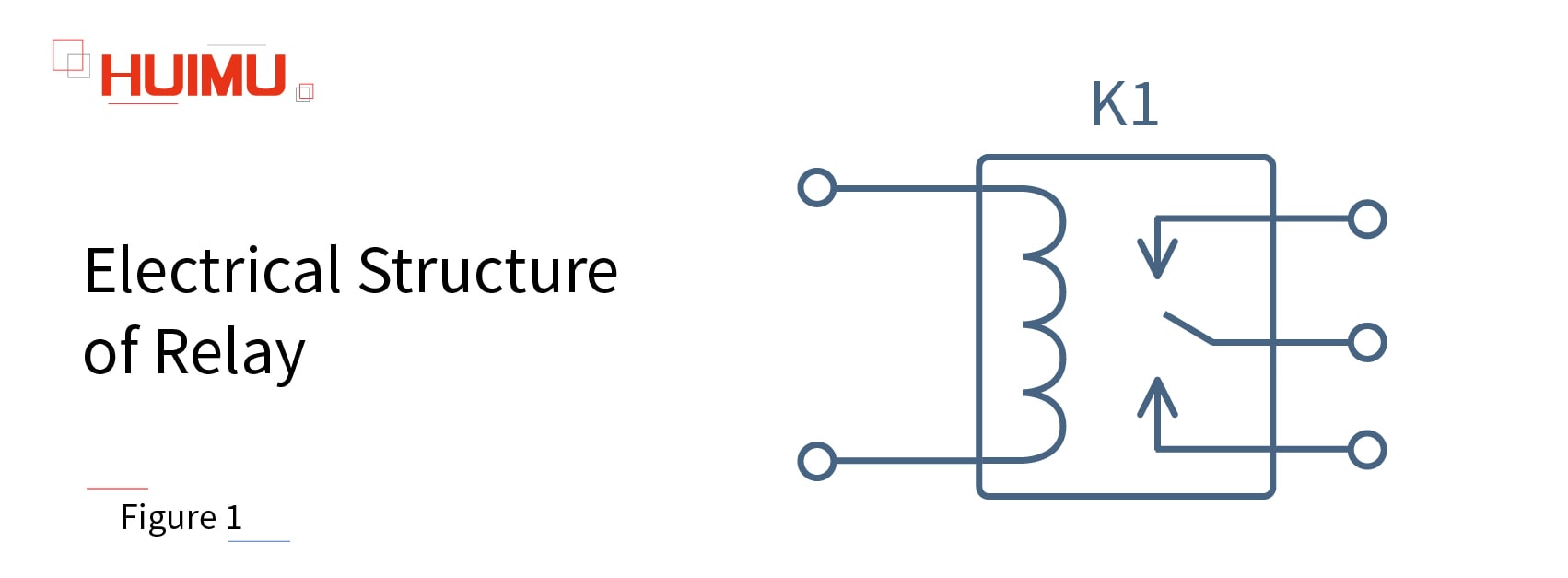
The Relay is an electronic control device that acts as an Electric Switch in almost all electrical and electronic equipment. When the input value reaches the set value, the output value will produce a step change in the output circuit, so the relays are typically used to control large output currents with low input currents. And the relays are also used for automatic adjustment (such as temperature control system), circuit protection and circuit switch.
According to the structure, the relays can be divided into mechanical relays (such as electromagnetic relay, electromechanical relay or EMR) and non-contact relays (solid state relay or SSR).
The working principle of the mechanical relay is the principle of electromagnetic induction. The structure of mechanical relay is very classic and has hardly changed since its invention, and consists of two parts: the coil and the contact.
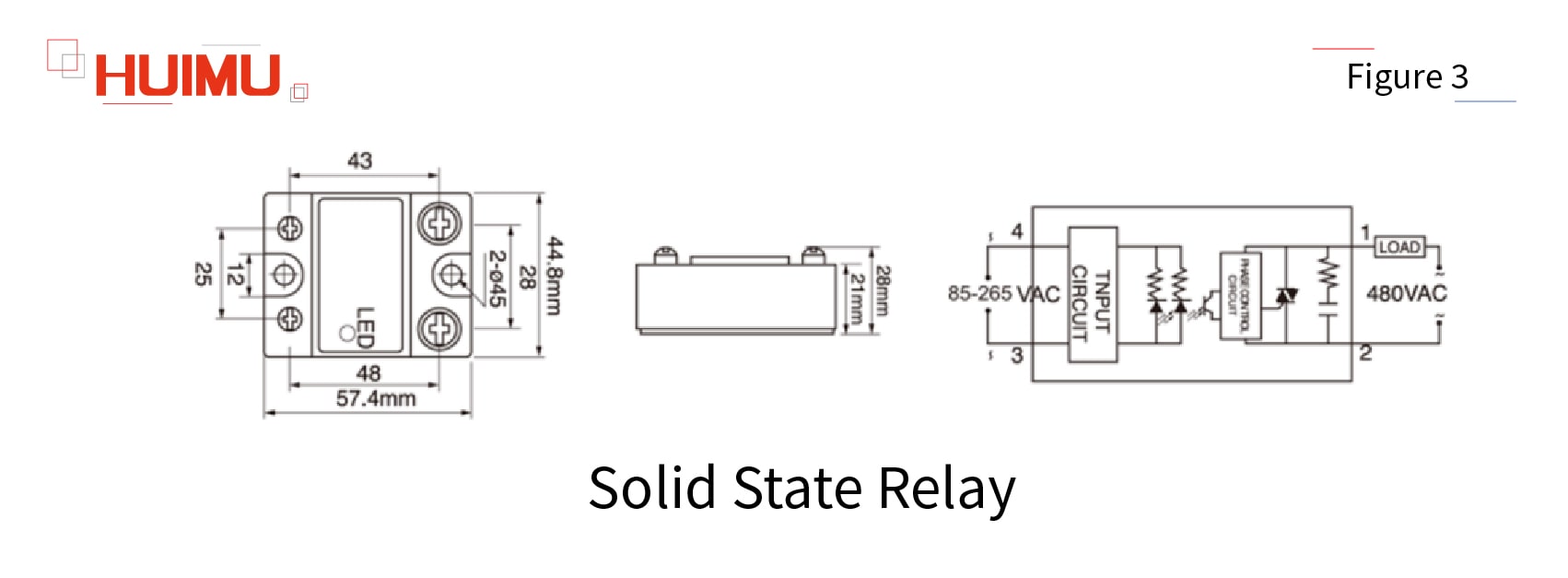
Click here to know more information about the solid state relays
With the development of science and technology, the demand for relays (small size, long service life, high stability, high performance, and high compatibility) is increasing, so the semiconductor components are used as the switching components in the relay. There are no mechanical contact and coil in such relays, which is different with the traditional mechanical relays.
Solid State Relays Introduction - 10.Attentions when Testing Solid-State Relays
§10. Attentions when testing Solid State Relays
1) First the relationship between the output current and the shell temperature (ambient temperature) should be known before testing to avoid permanent damage to the SSR caused by overload, because the rated output current will drop when the case temperature rises or with no radiator.
2) When testing the turn-on and turn-off voltage of DC-SSR, the input voltage cannot remain in the state between on and off for too long, otherwise the power consumption of the output terminal rises sharply and burns out the output switching components.
3) Do not arbitrarily speed up the action rate during the test (usually one period of the input signal should be more than 5 times the sum of the on/off times), otherwise the SSR relay will not work due to the large dynamic-switching-loss, or even the output switching components will be burnt out.
4) The solid state relays cannot achieve complete isolation between the output terminals in the off state, and there will be a certain leakage current at the output terminal. When the dielectric withstand voltage and insulation resistance are tested at a higher voltage, it is prone to electric shock, so the insulation resistance or the withstand voltage must not be tested on the output terminals.
Solid State Relays Introduction - 9.Attentions when Using or Installing Solid-State Relays
§9. Attentions when using or installing Solid State Relays
1) The actual application conditions of the product must fully comply with the requirements of the parameters and characteristic curves of solid-state relays.
2) SSR should not be used in applications with a large number of low or high harmonic components (for example, multiple sets of loads at the output of the inverter need to be switched separately). If the solid state relay is used in inverter as an electronic switch, because of the higher harmonics, the solid state relays may not be able to switch reliably, and the RC circuit inside the SSR relays will be exploded due to overheating.
3) The SSR relays should be kept away from strong electromagnetic interference sources and RF interference sources to ensure that the SSR can operate stably and safely, avoiding loss of control.
4) Except for the solid state relay with rated current of 1~5A which can be directly mounted on the printed circuit board, the other solid-state relays should be equipped with appropriate heat sinks. Thermal grease should be applied between the SSR base plate and the heat sink, and screwed tightly to make them close to each other for optimum heat dissipation. Or install a temperature control switch near the SSR relays backplane and the temperature control point is typically set between 75 °C and 80 °C.
5) When the input voltage of the input control signal is too high and exceeds the rated parameter of the SSR, the input resistor can be connected in series to the input circuit to reduce the excess value. Similarly, when the input current is too large, the shunt resistor can be connected in parallel to the input port.
6) The control signal and the load power supply need to be stable, and the fluctuation should not exceed 10%, otherwise the voltage regulation measures should be taken.
7) If using solid state relay to control the primary circuit of the transformer, the influence of the transient voltage of the secondary circuit on the primary circuit should be considered. In addition, since the current is asymmetrical in both directions, the transformer may also generate surge currents caused by saturation. In this case, the oscilloscope can be used to measure the inrush current and voltage that can be caused, so that the appropriate SSR and protection measures can be selected.
8) The output of the solid state relay is not completely isolated, when load power is applied to the output terminals, even if the solid-state relay does not operate, there will be some leakage current at the output terminals, which should be noted when using and designing the circuit. During maintenance, the service personnel must cut off the power supplies before checking the output circuit.
9) When a solid state relay needs to be replaced due to a fault, the SSR relay with the same model or technical parameters is recommended, to match the original application circuit and ensure reliable operation of the system.
Solid State Relays Introduction - 8.How to Select the Solid-State Relays
§8. How to select the Solid State Relays
The following are options to consider when selecting the appropriate solid-state relays based on the actual requirements:
1) Load Voltage - AC or DC
2) Load Current - Maximum Current and Minimum Current
3) Load Type - resistive, inductive or capacitive
4) Input Control Signal - AC or DC
5) Mounting Method - PCB, Panel or DIN rail mounting
6) Ambient Temperature - for calculating the Derating Factor and the size of the heat sink
7) International Certification – Underwriter Laboratories (UL), Canadian Standards Association (CSA), British Approvals Board of Telecommunications (BABT), Verband Deutscher Elektrotechniker (VDE), Technischen Uberwachungs Vereine (TUV), Conformite Europeene (CE) or other.
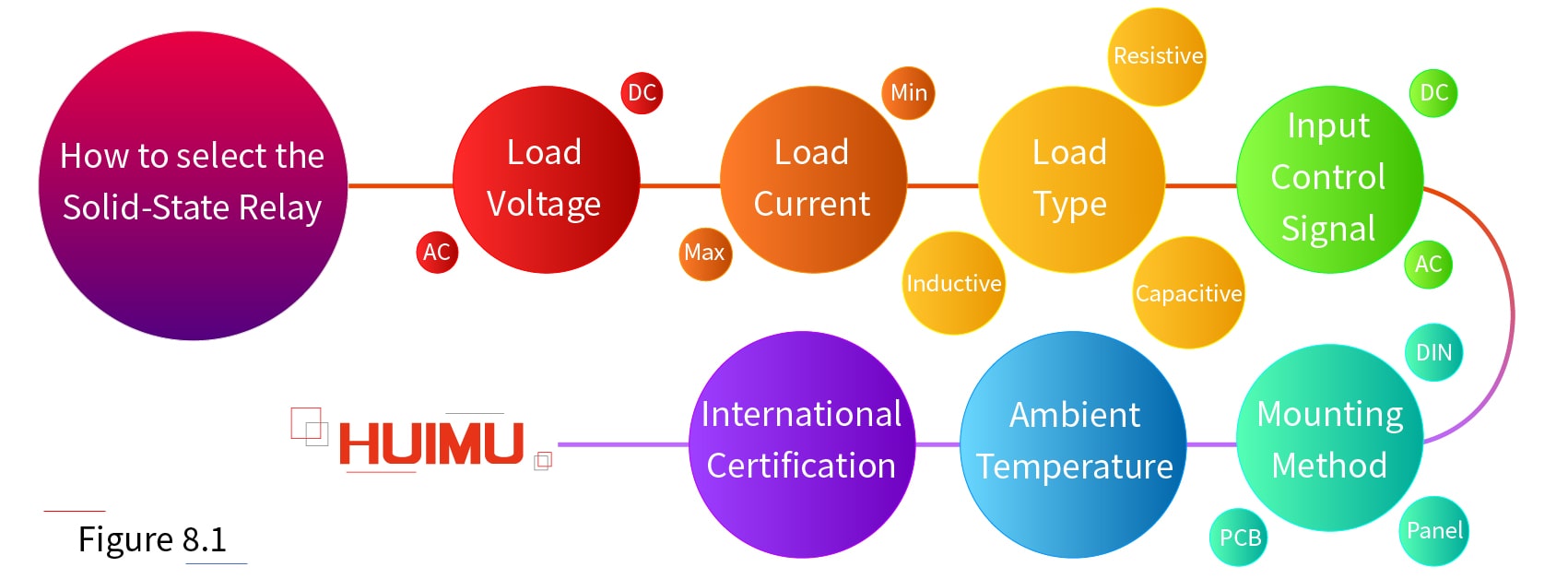
Load Voltage:
The first consideration is whether the load voltage is AC or DC to determine whether AC-SSR or DC-SSR is selected. Secondly, the voltage of the load power supply should be considered which cannot be larger than the output rating voltage, and less than the minimum voltage of the solid-state relay. Then consider the magnitude of the load voltage and the transient voltage. The load voltage refers to the steady-state voltage applied to the SSR switch output terminal, and the transient voltage refers to the maximum voltage that the output terminals of the SSR relays can withstand. When the AC inductive load, single-phase motor load or three-phase motor load is switched or energized, the voltage at the SSR switch output may be twice the peak voltage of the power supply, and this voltage cannot be greater than the transient voltage of the SSR to prevent the excessive shock voltage from damaging the electronic switch. Therefore, when selecting the SSR, it is best to leave a margin for the output voltage, and select the SSR relay with RC Circuit to protect the solid-state relay and optimize dv / dt.
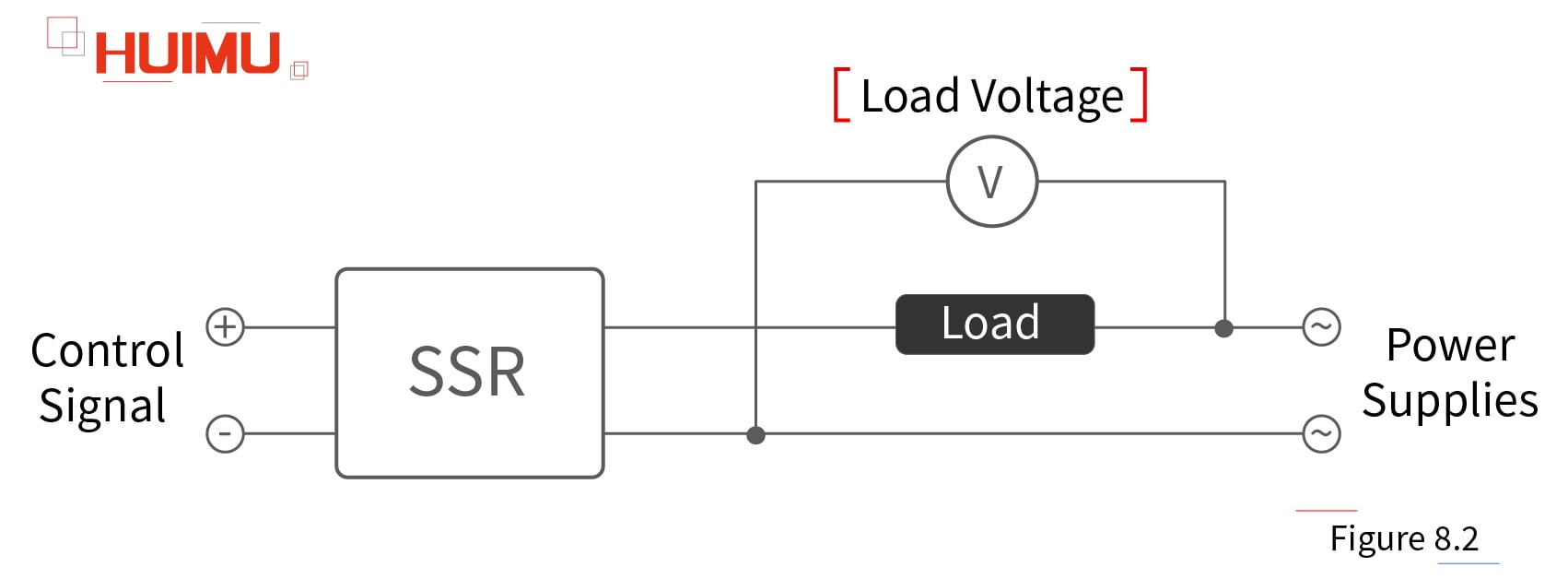
RC Circuit:
RC circuit, also known as RC filter, RC snubber, or RC network, is a circuit consisting of the resistor and the capacitor. It is recommended to select solid state relays with a varistor absorption circuit and an RC snubber circuit. The RC circuit blocks certain frequencies from passing and allows other frequency signals to pass to filter out the interfering signals. Moreover, the RC circuit can also be used to reduce the rise rate of the output voltage (dv/dt), to absorb the surge voltage, suppress excessive transient voltage / current, and prevent the solid-state relay from being broken due to overvoltage.
Load Current:
The output current value of the solid state relay is the steady-state current flowing through the output terminals of SSR, which is usually equal to the current of the load connected to the SSR output terminal. Since the switching elements of the SSR switches are very sensitive to temperature, and the overcurrent can generate a high amount of heat, so the overload capability of the SSR is weak. Therefore, the output current of the SSR relay shall not exceed its rated output current, and the surge current shall not exceed the overload capacity, especially for inductive/capacitive loads that are prone to generate surge currents, as well as the inrush current generated by the power supply itself.
The output current requires a margin to avoid excessive inrush currents that reduce the life of the solid-state relay. For general resistive loads, the rated effective operating current value can be selected based on 60% of the nominal value. Besides, the fast fuse and the air switch could be considered to protect the output loop, or add an RC sink loop and a varistor (MOV) to the output of the relay. The selection specification of varistor is to select 500V~600V MOV for 220VAC SSR, and 800V~900V MOV for 380VAC SSR.
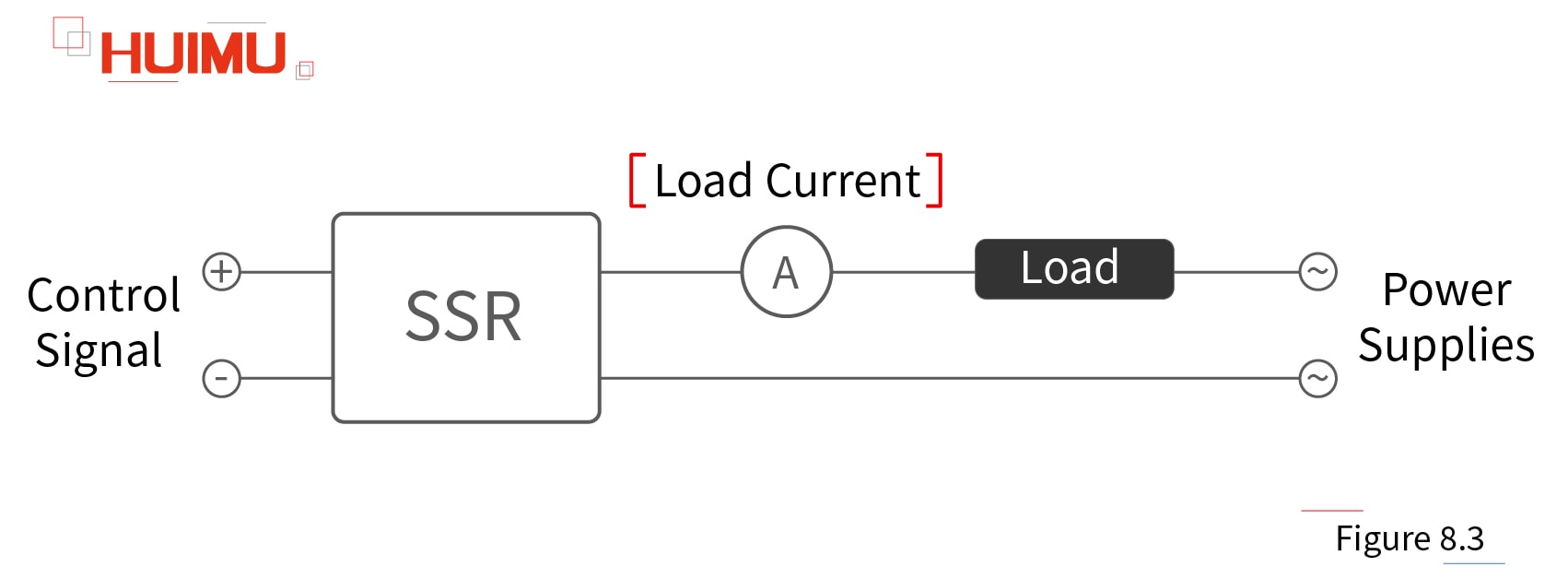
Inrush Current:
Almost all the controlled loads will generate large inrush currents at the moment of turn-on. For example:
1) The electric heating devices, like the incandescent lamps, and the electric furnaces, etc. They are purely resistive loads with a positive stability coefficient, but the resistance is small at a low temperature, so the current at startup will exceed several times the steady state current.
2) Some types of lamps have low impedance when burned off.
3) When the motor is turned on, rotor locked, and turned-off, it will generate large inrush current and voltage. The locked-rotor is a situation in which the motor still outputs torque when the speed is 0 rpm, at the meantime, the power factor of the motor will be extremely low, and the current can be up to 7 times of the rated current.
4) When the intermediate relay or solenoid valve is not closed reliably and bounce, it will also generate large inrush current.
5) When the capacitor bank or capacitor power supply are switched, there will cause a similar short circuit condition, and generate very large current.
6) When the capacitor commutated type motor is reversing, the capacitor voltage and the supply voltage are superimposed on output terminal of the SSR, and SSR will withstand a surge voltage twice the supply voltage.
Excessive inrush current can damage the semiconductor switches inside the SSR. Therefore, when selecting a relay, the surge characteristics of the controlled load should be analyzed first, so that the relay can withstand the inrush current while ensuring steady-state operation. The rated current of solid state relay should be selected according to the derating factor in actual requirements. And if the selected relay needs to work in a place with frequent operation, long life and high reliability, the rated current should be divided by 0.6 based on the known derating factor, to ensure the reliability of operation. Additionally, the resistor or inductor can be connected in series to the output loop to further limit the current.
Attention: Please do not use the SSR surge current value as the basis for selecting the load starting current. Because the SSR relay surge current value is based on the surge current of electronic switch with the precondition of half (or one) power supply cycle, that is 10ms or 20ms.
Load Type:
The loads can be divided into three types based on the electrical impedance: Resistive Load Type (or Pure Resistive Load), Inductive Load Type and Capacitive Load Type. There is no pure inductive load and pure capacitive load in the usual electrical appliances, because these two type loads don not do active power. In the series-parallel circuit, if the capacitive reactance is larger than the inductive reactance, the circuit is capacitive load; and vice versa.
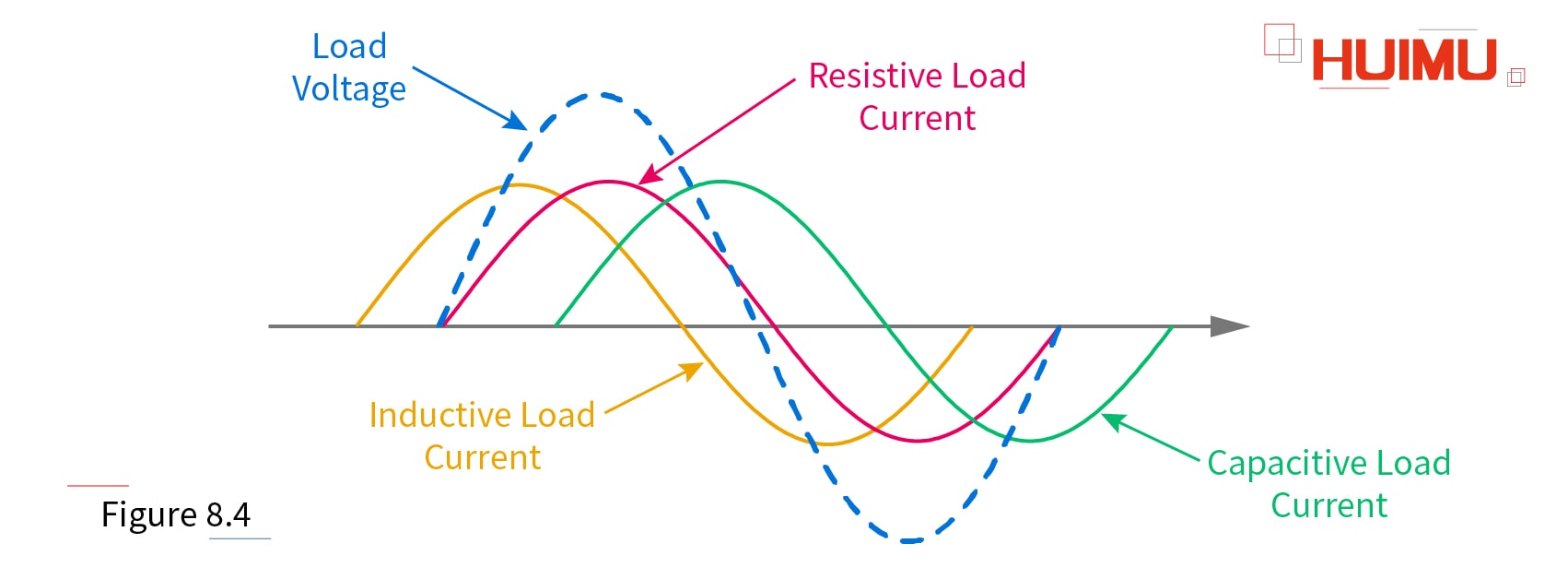
Resistive Load:
In a nutshell, a load that operates only by then resistor-type components is called the resistive load. However, some loads have low resistance at low temperatures, which results in a larger startup current. For example, when the electric furnace is just turned on, the current is 1.3-1.4 times larger than the stable current; when the incandescent lamp is turned on, the current is 10 times larger than the steady current.
Q1: What are the characteristics of the resistive load (when working)?
A1: In the DC circuit, the relationship between current and voltage is in accordance with the fundamental ohm's law, I=U/R; in an AC circuit, the current phase is the same as the phase of the voltage (compared to the power supply).
Q2: Which are resistive loads?
A2: Heating device that is heated by electric resistance (like resistance furnace, oven, electric water heater, hot oil, etc.), and lamps that rely on resistance wire to emit light (like iodine tungsten lamp, incandescent lamp, etc.).
Inductive Load:
Generally speaking, the inductive load is the load that applies the principle of electromagnetic induction (with inductance parameters), such as high-power electrical products (like refrigerators, air conditioners, etc.). The inductive load will increase the power factor of the circuit, and the current through the inductive load cannot abrupt change. At startup, the inductive load requires a much larger starting current (approximately 3-7 times) than the current required to maintain normal operation. For example, the starting current of an asynchronous motor is 5-7 times the rated value, and the starting current of the DC motor is slightly larger than the starting current of the AC motor; some metal-halide lamps have a turn-on time of up to 10 minutes, and their pulse currents up to 100 times steady state current.
Furthermore, when the power is turned on or off, the inductive load will produce a counter-electromotive force (usually 1-2 times the supply voltage), and the counter electromotive force(abbreviated counter EMF or simply CEMF) will be superimposed with the power supply voltage, and the resulting voltage is up to three times the supply voltage. So, when the load type is an inductive load, the output terminal of solid-state relay should connect a varistor with a withstand voltage of 1.6-1.9 times the load voltage. The counter EMF is an indefinite value that varies with L and di/dt, and if the current rate of change (di / dt) is too high, the SSR will be damaged. In practical applications, CEMF can be reduced by series inductance L, and the magnitude of the L inductance depends on the size and cost.
Q3: What are the characteristics of the inductive load (when working)?
A3: Inductive loads are lagging (current lags voltage). In the DC circuit, the inductive load allows current to flow through and energy to be stored in the inductor, and the current lags behind the voltage. In the AC circuit, the current phase lags behind the voltage phase (compared to the power supply), and the phase can lag a quarter cycle (or 90 degrees) at the maximum.
Q4: Which are inductive loads?
A4: Lamps that rely on energized gas to emit light (like daylight lamps, high-pressure sodium lamps or HPS lamps, mercury lamps, metal-halide lamps, etc.), and high-power electrical equipment (like motor-based equipment, compressors, relays, etc.).
Capacitive Load:
Generally, a load with a capacitance parameter is called the capacitive load, and the capacitive load will reduce the power factor of the circuit. During charging or discharging, the capacitive load is equivalent to a short circuit because the voltage across the capacitor cannot be changed abruptly.
Q5: What are the characteristics of the inductive load (when working)?
A5: Capacitive loads are leading (current leads voltage). In the DC circuits, capacitive loads prevent current from flowing, but can store energy. In the AC circuits, the current phase leads the voltage phase (compared to the power supply), and the phase can lead a quarter cycle (or 90 degrees) at the maximum.
Q6: Which are inductive loads?
A6: Device with a capacitor, such as a compensation capacitor. And power control devices such as switching power supplies, IT equipment and etc.
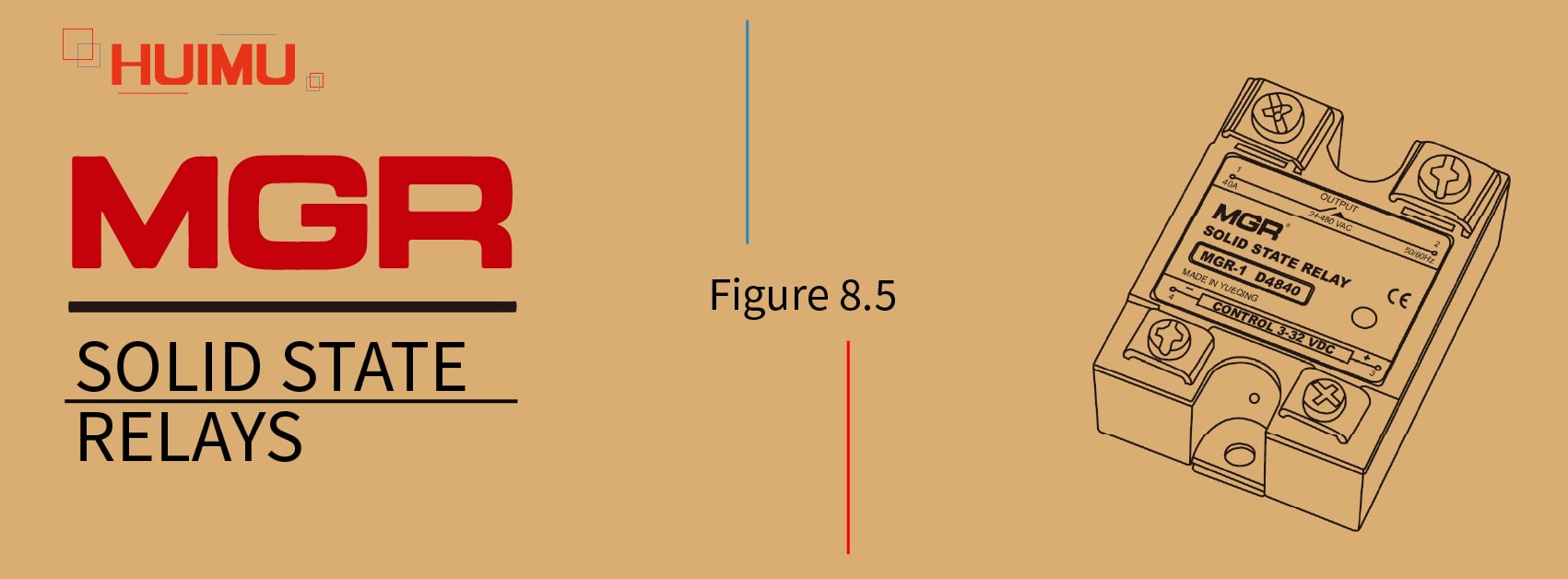
How to choose Solid-State Relay according to load type
1) For inductive and capacitive loads, a solid-state relay with a higher dv/dt is recommended, if there is a biggish dv/dt (voltage exponential rise rate) applied to the relay’s output terminal during the AC solid state relay turning on/off.
2) For AC resistive loads and most AC inductive loads, zero-crossing relays are available to extend the life of load and relay, and reduce their own RF interference.
3) As a phase output controller, a random type solid state relay should be used.
* Power Factor:
In electrical engineering, the power factor of an AC power system is defined as the ratio of the real power flowing to the load to the apparent power in the circuit, and is a dimensionless number in the closed interval of -1 to 1. If it is not specified the load power of the general product is the apparent power (includes both active power and reactive power). But the general specification of the inductive load often gives the magnitude of active power. For example, although a fluorescent lamp is labeled 15 to 40 watts (its active power), its ballast consumes approximately 8 watts of power, so 8W should be added to 15~40w to calculate the total power. The inductive portion of the product (i.e. the amount of reactive power) can be calculated from the given power factor.
Input Control Signal:
1) Input Control Voltage: the input control voltage has a wide range of 3~32V.
2) Input Control Current: the input current of DC SSRs and AC single-phase SSRs is generally around 10mA, and the input current of AC three-phase SSRs is generally around 30mA, which also can be customized to be less than 15mA.
3) Control Frequency: the control operating frequency of AC solid state relays generally does not exceed 10HZ, and the DC solid state relay control signal period should be greater than five times the sum of the relay's "on time" and "off time".
Mounting Method:
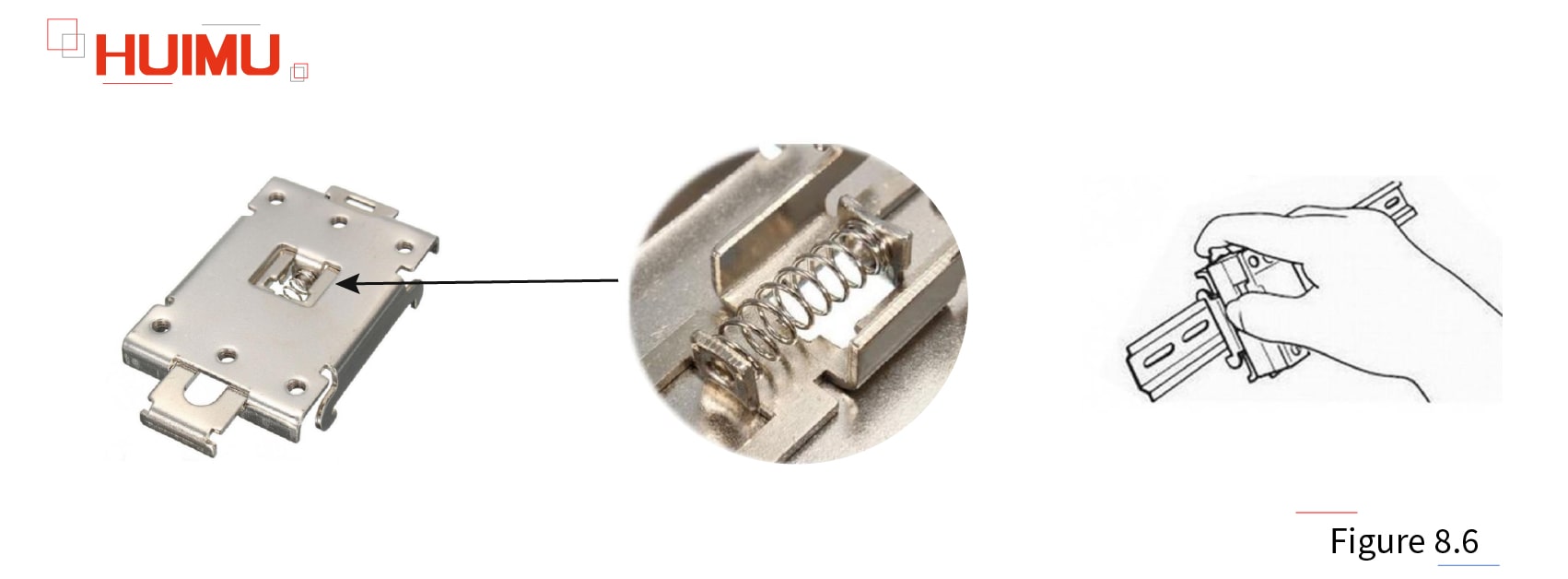
In many cases, the load power will limit whether the SSR is mounted on the PCB, the panel or the DIN rail.
Ambient Temperature:
When the relay is in the on state, it will withstand the dissipated power of P = V (on-state voltage drops) × I (load current), and the load capacity of the SSR is greatly affected by the ambient temperature and its own temperature. If the ambient temperature is too high, the load capacity of the SSR will inevitably decrease accordingly, moreover, the SSR switch may be out of control, or even be permanently damaged. Therefore, it is necessary to set a certain margin according to the actual working environment, and select the appropriate heat sink size to ensure the heat dissipation conditions. For load currents greater than 5A, a heat sink should be installed. For currents above 100A, the heat sink and fan should be equipped for strong cooling. If the SSR relay is operated at high temperatures (40 ° C ~ 80 ° C) for a long time, the load current can be reduced according to the maximum output current and ambient temperature curve provided by the manufacturer to ensure normal operation, and the load current is usually controlled within 1/2 of the rated value.
* Derating Factor:
The table below shows the recommended derating factor for the rated output current of solid-state relays applied on various loads at room temperature (the overload capability and the load surge current have been considered).
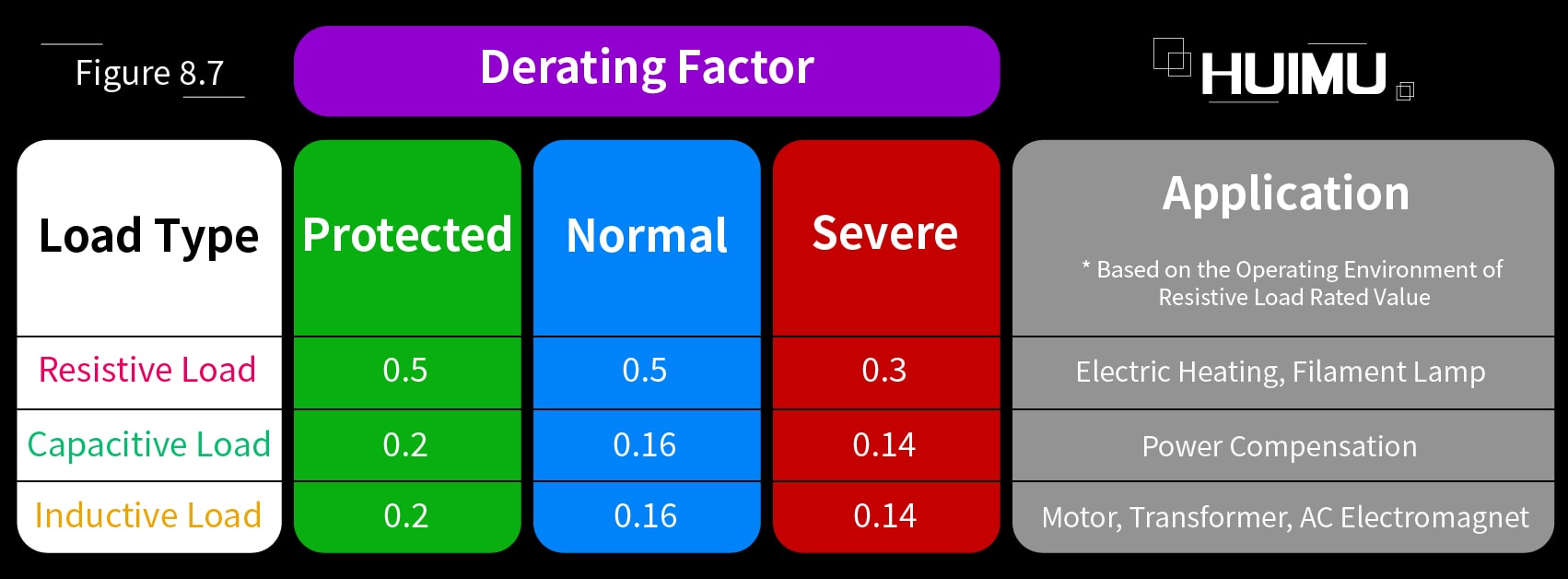
There are two ways to use the derating factor:
1) The rated current value of the solid state relay can be selected according to the derating factor of different environments and different load types. The rated current of the SSR relay is equal to the continuous current value of the load divided by the derating factor.
2) If the solid-state relay has been selected and the load type or environment changes, the load current should be adjusted based on the load curve and the derating factor in certain environment. The adjusted current multiplied by the derating factor must be lower than the rated value of the solid state relay.
In addition, when SSRs are run in applications that require more frequent operation, longer life, and more stable reliability performance, the derating factor needs to be further multiplied by 0.6 based on the data in the table. However, the load current should not be lower than the minimum output current of the solid state relay, otherwise the relay will not be switched on or the output state will be abnormal.
MGR-AH_3 Series Panel Mount Solid State Relay
MGR-AH_3 Series Panel Mount Solid State Relay [All the information on this website is for reference only, and the actual product and the a...
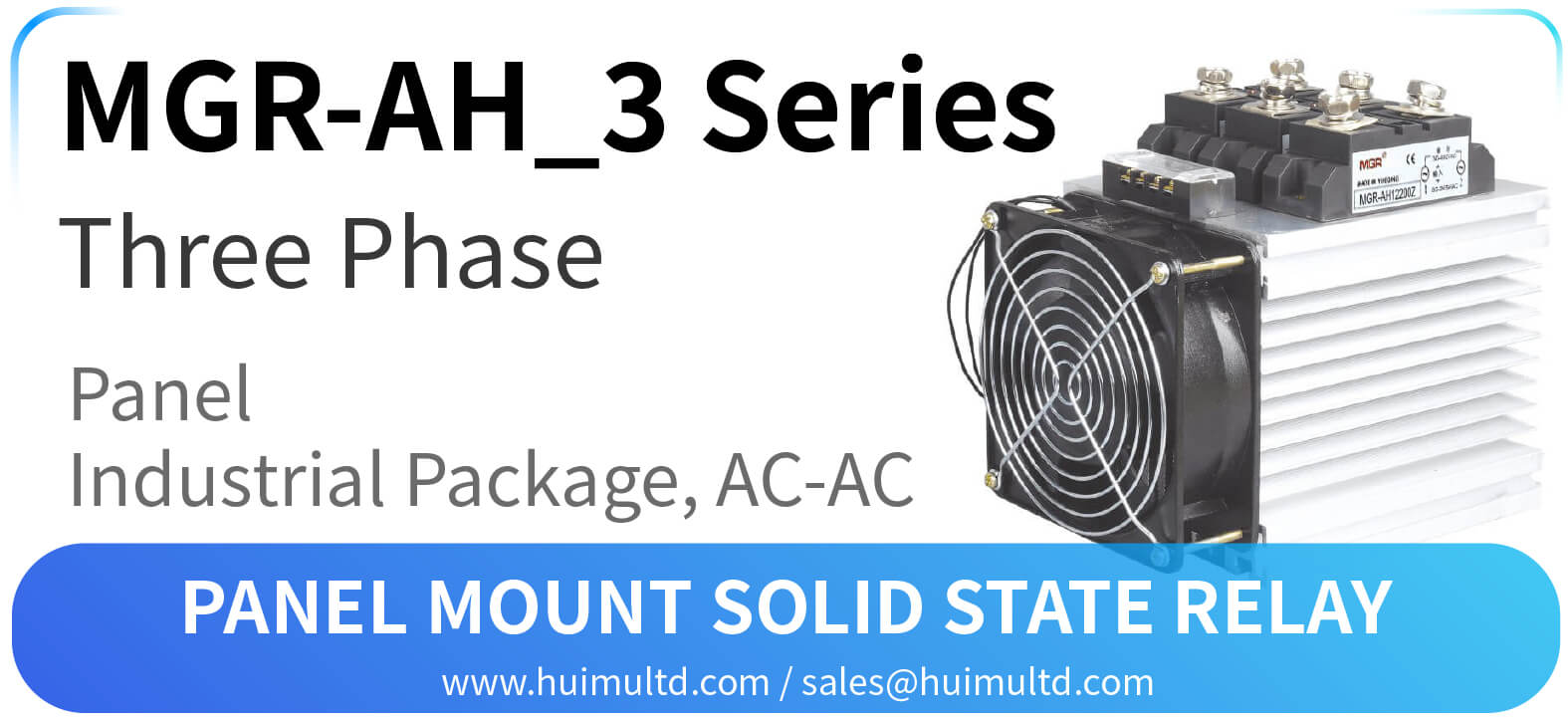
-
§1. What is SPDT Switch SPDT (Single Pole Double Throw) is a special switch structure. Different with the normal SPST (Single Pole Single ...
-
MGR-R Series Voltage Power Regulator [All the information on this website is for reference only, and the actual product and the accompanyi...
-
MGR-H Series Panel Mount Solid State Relay [All the information on this website is for reference only, and the actual product and the acco...